A lo largo de los años, la propia necesidad de reducir la dependencia de energías no renovables, ha ido modelando la fabricación de motores de los automóviles. En los primeros vehículos de la historia esta no era una preocupación de los fabricantes… y siguió sin serlo hasta mediados de los años 70, con la crisis del petróleo.
no podían desperdiciar así los combustibles fósiles. Era necesaria una acción urgente y progresiva, que fuese reduciendo el consumo desmesurado de combustible. De este modo, los sistemas de coches de gasolina han ido evolucionando desde el derroche, hasta ser mucho más eficientes. Este ha sido el camino hacia unos motores cada vez más frugales y menos contaminantes:
no podían desperdiciar así los combustibles fósiles. Era necesaria una acción urgente y progresiva, que fuese reduciendo el consumo desmesurado de combustible. De este modo, los sistemas de coches de gasolina han ido evolucionando desde el derroche, hasta ser mucho más eficientes. Este ha sido el camino hacia unos motores cada vez más frugales y menos contaminantes:
Fue entonces cuando sociedad y fabricantes se dieron cuenta de que
1- el primer sistema de inyeccion electronica que salió fue el TBFI ( throtle body fuel injection ), le decian tambien carburador electronico. tenia uno o dos inyectores antes del manifold de entrada del aire al motor. en el mismo lado donde estaba el antiguo carburador.
2- despues salió el sistema de inyeccion electronica multipunto EFI ( electronic fuel injection ) que ya constaba de 4 inyectores en cada entrada del manofold de entrada del aire al motor.
3- despues salió el sistema de inyeccion electronica secuencial SEFI ( secuential electronic fuel injection ), casi lo mismo del EFI pero este sistema inyecta la gasolina cuando la valvula de admision de aire se abre.
4- ahora ha salido el sistema de inyeccion electronica GDI ( gasoline direct injection ), ahora la gasolina se inyecta directamente en el cilindro, no como los otros sistemas que lo hacen de manera indirecta por la valvula de admision. estos motores son muy economicos en el consumo de gasolina, mejor que todos los sistemas anteriores.
5-por ultimo esta el sistema de inyeccion electronica CRDI-D ( common rail direct injection-diesel ), osea, riel comun de inyeccion directa diesel. tambien parecido al GDI solo que inyecta combustible diesel.
1- el primer sistema de inyeccion electronica que salió fue el TBFI ( throtle body fuel injection ), le decian tambien carburador electronico. tenia uno o dos inyectores antes del manifold de entrada del aire al motor. en el mismo lado donde estaba el antiguo carburador.
2- despues salió el sistema de inyeccion electronica multipunto EFI ( electronic fuel injection ) que ya constaba de 4 inyectores en cada entrada del manofold de entrada del aire al motor.
3- despues salió el sistema de inyeccion electronica secuencial SEFI ( secuential electronic fuel injection ), casi lo mismo del EFI pero este sistema inyecta la gasolina cuando la valvula de admision de aire se abre.
4- ahora ha salido el sistema de inyeccion electronica GDI ( gasoline direct injection ), ahora la gasolina se inyecta directamente en el cilindro, no como los otros sistemas que lo hacen de manera indirecta por la valvula de admision. estos motores son muy economicos en el consumo de gasolina, mejor que todos los sistemas anteriores.
5-por ultimo esta el sistema de inyeccion electronica CRDI-D ( common rail direct injection-diesel ), osea, riel comun de inyeccion directa diesel. tambien parecido al GDI solo que inyecta combustible diesel.
INTRODUCCION
Sistema de inyección a gasolina T.B.I.
Se conoce como T B I al Sistema que inyecta el combustible en el cuerpo de aceleración, utiliza 1 o 2 inyectores eléctricos, colocados en la parte superior del cuerpo de aceleración. El TBI es el sustituto del carburador.
El sistema de inyección al cuerpo de aceleración TBI (Throttle Body Inection) de GM fue introducido en 1982 en el motor 2.5L 4 cilindros y en los motores de 5.0 y 5.7L V8. Los motores de 4 cilindros usaban una unidad TBI con un solo inyector, montada en el cuerpo de aceleración. El primer sistema TBI para motores V8 tenia dos unidades cada una con un solo inyector, este sistema fue llamado Cross Fire Injection.

En el sistema TBI de la GM se emplea una computadora dentro del vehículo para regular la relación del aire y el combustible. Se trata de una versión modificada de la computadora 3C que se emplea en los motores de 1981. El Módulo de Control Electrónico (ECM) vigila la posición del acelerador, las rpm del motor, la presión absoluta del múltiple (MAP), la temperatura del refrigerante, la velocidad del vehículo y el nivel del oxígeno en el escape. El ECM luego compara esta información con su memoria pregrabada y calcula la mezcla de aire y combustible precisa para reducir aun mínimo las emisiones del escape y producir una potencia máxima. El ECM luego transmite una señal al inyector (o inyectores), para indicarle cuándo y por cuánto tiempo debe inyectar combustible dentro del múltiple de admisión. Al mismo tiempo, ajusta la sincronización del encendido. El sistema TBI consiste en una bomba de combustible instalada en el tanque, el ECM, el inyector (o inyectores), filtros de combustibles y conductos de suministro y retorno. Se usan dos tipos de inyectores: de una sola perforación y de dos perforaciones. Se emplea la unidad de u
na sola perforación en motores pequeños como el L-4. Los motores V6 y V8 y de tamaño mayor utilizan una unidad de doble perforación o dos unidades de una sola perforación.
UNDIDAD TBI: consiste de ensambles principales, el cuerpo de dosificación de combustible y el cuerpo de aceleración. Dependiendo del motor el cuerpo de dosificación de combustible tiene una garganta y un inyector o doble garganta y dos inyectores. Además de los inyectores el cuerpo de dosificación contiene al regulador de presión. El sensor de de posición del acelerador(TP), la valvula IAC y los puertos de vacio para componentes como el sensor MAP, la valvula EGR, y el sistema EVAP, están localizados en el cuerpo de aceleración.
TAREA 1 "DESCRIPCION DE SUS PARTES/COMPONENTES INTERNOS Y FUNCION"




TAREA 2 "DESCRIPCION DE TP Y IAC DEL SISTEMA DE INYECCION TBI"
a) SENSOR DE POSICION DEL ACELERADOR (TP)
El sensor de posición del acelerador es un sensor de tres cable, una resistencia variable (potenciómetro) montado en el cuerpo de aceleración y accionado por la flecha de la válvula del acelerador. Cuando el acelerador está cerrado el ECM registra una señal de voltaje bajo, cuando el acelerador está totalmente abierto el ECM registra una señal de voltaje alto. Esto quiere decir, que la señal del voltaje cambia en relación a la posición del acelerador, en marcha mínima alrededor de0.5 volts y en acelerador totalmente abierto de 4.5 a 5 volts
b) VALVULA DE CONTRO DE AIRE EN MARCHA MÍNIMA (IAC)
La válvula de control del aire de marcha mínima está localizada en el cuerpo de aceleración, permite que entre aire al motor, por un pasaje alterno al obturador del acelerador, y como su nombre lo dice controla la cantidad de aire que entra al motor en ma
rcha mínima. La válvula IAC consiste de un vástago movible, impulsado por un pequeño motor eléctrico llamado motor de pasos. el ECM usa a la válvula IAC para controlar las rpm de marcha mínima,
esto lo hace cambiando la posición del vástago en el conducto del aire de marcha mínima en el cuerpo de aceleración. Este varía el flujo de aire que pasa alrededor de la mariposa del acelerador, cuando el acelerador está cerrado .
TAREA 3 "QUE ES EL MANTENIMIENTO AL SISTEMA DE INYECCION TBI"
El mantenimiento y reparación de inyectores es un conjunto de operaciones, verificaciones y cuidados necesarios para que en un futuro no se existan fallas en el inyector o inyectores.
Consiste en:
MANTENIMIENTO PREVENTIVO; que es aquel que dispone con anticipación la falla de cualquier objeto.
MANTENIMIENTO CORRECTIVO; es aquel que repara, atenúa o subsana cualquier objeto con falla presente este está establecido por el mantenimiento por laboratorio y mantenimiento empleando la boya.
PROCESOS
a) VALORES Y MEDICION DE LOS CIRCUITOS DE (
VOLTAJE Y RESISTENCIA)
TP


IAC

b) MANTENIMIENTO AL SISTEMA DE INYECCION TBI
*MANTENIMIENTO EMPLEANDO LA BOYA:
Herramientas:
Boya
Liquido para lavar inyectores
Compresora de aire
Adaptadores para conectar al riel de inyectores
Ahorcadores de manguera
Adaptador para manguera
Manguera adaptada ala línea de comb. y boya
P R O C E D I M I E N T O
1.- Se localiza el fusible o el conector de la bomba de combustible, y se desconecta ya sea el fusible o conector, esto para que la bomba de combustible no envié gasolina al riel de inyectores. Para saber si deja de funcionar la bomba, el automóvil debe estar encendido, se prosigue a desconectar el fusible o conector de la bomba de combustible y el automóvil va a ir bajando sus revoluciones hasta apagarse. Si no se localiza el fusible y conector de la bomba de combustible, entonces en el riel de inyectores se hace un puente con un adaptador o ahorcador, esto para que circule el liquido en círculos.
2.- Después ya teniendo la boya se abre su deposito para agregar el liquido lava inyectores y se cierra.
3.- Se quita el tapón de la línea de comb. y se le coloca el adaptador de la boya, se conecta la boya al adaptador que se puso en el riel de inyectores ya con el líquido lava inyectores entre unos 300ml a 500ml
4.- La boya es colgada en un lugar estratégico, y se le conecta la manguera de la compresora a su entrada de aire
5.-Después se ponen las psi requeridas esto dependiendo del manual, y se abre la llave de paso. Y se pone atención de que no vaya a haber ninguna fuga de aire y liquido.
6.- Ahora si se hecha a andar el vehiculo
7.- Después de 15 a 25 minutos se acelera un poco y si se quiere apagar quiere decir que se ha terminado el liquido lava inyectores, y ya los inyectores están limpios
8.- Se apaga el automóvil, se retira la boya, adaptadores y ahoracadores que se utilizaron para puentear (en caso si se usaron), y se vuelve a conectar el fusible o conector de la bomba de combustible
9.- Se enciende el automóvil y se verifica, observa y escucha que este en buen funcionamiento
* MANTENIMIENTO EMPLEANDO EL ULTRA SONIDO (LABORATORIO)
Herramientas:
Equipo de laboratorio
Liquido lava inyectores
Tinta especial
Bandeja de metal
P R O C E D I M I E N T O
1.- Desmontar el inyector del motor. Esto se consigue aflojando los tornillos del cuerpo de aceleración. En muchos casos suelen tener una traba, retire las trabas de a una. Estas trabas suelen estar colocadas en una ranura que tiene el cuello de cada inyector. Preste atención a la ranura. A veces algunos inyectores tienen dos ranuras y la traba. Siempre va colocada en la ranura superior. La Flecha indica la ranura donde va colocada la traba de sujeción La Flecha indica la ranura donde va colocada la traba de sujeción
2.- Una vez desmontado el inyector, límpielo primeramente por fuera, use para esto cualquier desengranaste o un poco de gasolina. Esto evitara que Ud. mismo ensucie el liquido en el equipo de ultrasonido
3.- Coloque el inyector en el equipo de ultrasonido y simultáneamente conecte el generador de pulsos. Ponga en funcionamiento el equipo de ultrasonido
4.- Deje funcionando el equipo de ultrasonido por unos 15 minutos, luego de este tiempo saque el inyector del liquido y sopleteelos ingresando el aire comprimido por la boca de acceso del combustible a los inyector. Para que el aire pase por dentro de los inyector, el generador debe estar funcionando
5.- Repita el procedimiento nuevamente. Desde el punto 3
6.- Lubricación interna del inyector. Cambio o lubricación de O rings de inyector.
7.-. Balance, calibración de inyectores. Control, revisión, limpieza y puesta a punto del sistema de inyección. Evaluación completa del sistema de inyección. Diagnóstico, revisión y control de la presión de combustible.
8.- Se colocan nuevamente asegurándose de que esté bien fijo el riel y se echa a andar para observar de que no exista falla.
RECURSOS
PARA EL DESARROLLO DEL PROYECTO "SISTEMA DE INYECCION DE COMBUSTIBLE T.B.I."
- MATERIALES
1. PC (computadora)
2. Memoria USB
3. CD (disco compacto)
- BIBLIOGRAFICOS
1. Libro: GM 1995, INYECCION DE COMBUSTIBLE, GM, MEXICO DF.
2. PAGINAS WEB
http://automecanico.com/
http://www.autoelectronico.com/
http://www.todomecanica.com/
http://www.mecanicavirtual.org/
http://www.mimecanicapopular.com/
http://autorepair.about.com/
http://www.autocity.com/
http://www.bloghella.com.mx/
- INSUMOS
1. Hrs. de Internet 15=$120
2. Impresiones 32 = $32
3. CD 2 = $12
4. Copias 14= $7
TOTAL= $171.00
CONLUSIONES
Se sabe, que la combustión en un motor es lo que determina el tiempo de vida de éste; así como la vida de todos los que habitamos este planeta, o sea que si la combustión permite la expulsión de gases altamente contaminantes, estaríamos dañando a nuestro planeta en forma muy veloz.Por esta razón tanto un carburador como el sistema TBI; funcionan sobre la base de una mezcla precisa de aire y combustible (14,7 partes de aire por 1 de combustible).
El carburador permite el ajuste manual de esta mezcla por lo cual un dispositivo mal regulado podría ser altamente nocivo. Dentro de la tolerancia 12 a 1 (mezcla rica en combustible); o 16 a 1 (mezcla pobre en combustible), es posible obtener diferentes resultados. Si se ajusta a una mezcla muy rica se pueden dañar las válvulas y pistones; y si se ajusta a muy pobre el motor pierde fuerza.Si la mezcla no es la correcta, tenemos una de las causas de un motor "desafinado" con lo cual el motor estaría sufriendo daños, y/o contaminando el medio ambiente.
El sistema TBI, en base a un monitoreo constante de sensores colocados en diferentes partes del motor, ajusta la mezcla, obedeciendo a un programa de su computadora de a bordo de tal manera que la entrega de la mezcla aire-combustible siempre sea la correcta.Pero cabe mencionar que un sistema de inyección TBI no es un eficiente al 100% en cuanto a la inyección, es por eso que en el transcurso de los años las compañías automotrices desarrollan sistema aun mas tecnológicos “en toda la extensión de la palabra” para la sociedad.
Publicado por alex9 en 11:50 No hay comentarios:
Sistema de inyección a gasolina T.B.I.
Se conoce como T B I al Sistema que inyecta el combustible en el cuerpo de aceleración, utiliza 1 o 2 inyectores eléctricos, colocados en la parte superior del cuerpo de aceleración. El TBI es el sustituto del carburador.
El sistema de inyección al cuerpo de aceleración TBI (Throttle Body Inection) de GM fue introducido en 1982 en el motor 2.5L 4 cilindros y en los motores de 5.0 y 5.7L V8. Los motores de 4 cilindros usaban una unidad TBI con un solo inyector, montada en el cuerpo de aceleración. El primer sistema TBI para motores V8 tenia dos unidades cada una con un solo inyector, este sistema fue llamado Cross Fire Injection.

En el sistema TBI de la GM se emplea una computadora dentro del vehículo para regular la relación del aire y el combustible. Se trata de una versión modificada de la computadora 3C que se emplea en los motores de 1981. El Módulo de Control Electrónico (ECM) vigila la posición del acelerador, las rpm del motor, la presión absoluta del múltiple (MAP), la temperatura del refrigerante, la velocidad del vehículo y el nivel del oxígeno en el escape. El ECM luego compara esta información con su memoria pregrabada y calcula la mezcla de aire y combustible precisa para reducir aun mínimo las emisiones del escape y producir una potencia máxima. El ECM luego transmite una señal al inyector (o inyectores), para indicarle cuándo y por cuánto tiempo debe inyectar combustible dentro del múltiple de admisión. Al mismo tiempo, ajusta la sincronización del encendido. El sistema TBI consiste en una bomba de combustible instalada en el tanque, el ECM, el inyector (o inyectores), filtros de combustibles y conductos de suministro y retorno. Se usan dos tipos de inyectores: de una sola perforación y de dos perforaciones. Se emplea la unidad de u

UNDIDAD TBI: consiste de ensambles principales, el cuerpo de dosificación de combustible y el cuerpo de aceleración. Dependiendo del motor el cuerpo de dosificación de combustible tiene una garganta y un inyector o doble garganta y dos inyectores. Además de los inyectores el cuerpo de dosificación contiene al regulador de presión. El sensor de de posición del acelerador(TP), la valvula IAC y los puertos de vacio para componentes como el sensor MAP, la valvula EGR, y el sistema EVAP, están localizados en el cuerpo de aceleración.
TAREA 1 "DESCRIPCION DE SUS PARTES/COMPONENTES INTERNOS Y FUNCION"




TAREA 2 "DESCRIPCION DE TP Y IAC DEL SISTEMA DE INYECCION TBI"
a) SENSOR DE POSICION DEL ACELERADOR (TP)
El sensor de posición del acelerador es un sensor de tres cable, una resistencia variable (potenciómetro) montado en el cuerpo de aceleración y accionado por la flecha de la válvula del acelerador. Cuando el acelerador está cerrado el ECM registra una señal de voltaje bajo, cuando el acelerador está totalmente abierto el ECM registra una señal de voltaje alto. Esto quiere decir, que la señal del voltaje cambia en relación a la posición del acelerador, en marcha mínima alrededor de0.5 volts y en acelerador totalmente abierto de 4.5 a 5 volts
b) VALVULA DE CONTRO DE AIRE EN MARCHA MÍNIMA (IAC)
La válvula de control del aire de marcha mínima está localizada en el cuerpo de aceleración, permite que entre aire al motor, por un pasaje alterno al obturador del acelerador, y como su nombre lo dice controla la cantidad de aire que entra al motor en ma
esto lo hace cambiando la posición del vástago en el conducto del aire de marcha mínima en el cuerpo de aceleración. Este varía el flujo de aire que pasa alrededor de la mariposa del acelerador, cuando el acelerador está cerrado .
TAREA 3 "QUE ES EL MANTENIMIENTO AL SISTEMA DE INYECCION TBI"
El mantenimiento y reparación de inyectores es un conjunto de operaciones, verificaciones y cuidados necesarios para que en un futuro no se existan fallas en el inyector o inyectores.
Consiste en:
MANTENIMIENTO PREVENTIVO; que es aquel que dispone con anticipación la falla de cualquier objeto.
MANTENIMIENTO CORRECTIVO; es aquel que repara, atenúa o subsana cualquier objeto con falla presente este está establecido por el mantenimiento por laboratorio y mantenimiento empleando la boya.
PROCESOS
a) VALORES Y MEDICION DE LOS CIRCUITOS DE (
TP

IAC

b) MANTENIMIENTO AL SISTEMA DE INYECCION TBI
*MANTENIMIENTO EMPLEANDO LA BOYA:
Herramientas:

Boya
Liquido para lavar inyectores
Compresora de aire
Adaptadores para conectar al riel de inyectores
Ahorcadores de manguera
Adaptador para manguera
Manguera adaptada ala línea de comb. y boya
P R O C E D I M I E N T O
1.- Se localiza el fusible o el conector de la bomba de combustible, y se desconecta ya sea el fusible o conector, esto para que la bomba de combustible no envié gasolina al riel de inyectores. Para saber si deja de funcionar la bomba, el automóvil debe estar encendido, se prosigue a desconectar el fusible o conector de la bomba de combustible y el automóvil va a ir bajando sus revoluciones hasta apagarse. Si no se localiza el fusible y conector de la bomba de combustible, entonces en el riel de inyectores se hace un puente con un adaptador o ahorcador, esto para que circule el liquido en círculos.
2.- Después ya teniendo la boya se abre su deposito para agregar el liquido lava inyectores y se cierra.
3.- Se quita el tapón de la línea de comb. y se le coloca el adaptador de la boya, se conecta la boya al adaptador que se puso en el riel de inyectores ya con el líquido lava inyectores entre unos 300ml a 500ml
4.- La boya es colgada en un lugar estratégico, y se le conecta la manguera de la compresora a su entrada de aire
5.-Después se ponen las psi requeridas esto dependiendo del manual, y se abre la llave de paso. Y se pone atención de que no vaya a haber ninguna fuga de aire y liquido.
6.- Ahora si se hecha a andar el vehiculo
7.- Después de 15 a 25 minutos se acelera un poco y si se quiere apagar quiere decir que se ha terminado el liquido lava inyectores, y ya los inyectores están limpios
8.- Se apaga el automóvil, se retira la boya, adaptadores y ahoracadores que se utilizaron para puentear (en caso si se usaron), y se vuelve a conectar el fusible o conector de la bomba de combustible
9.- Se enciende el automóvil y se verifica, observa y escucha que este en buen funcionamiento
* MANTENIMIENTO EMPLEANDO EL ULTRA SONIDO (LABORATORIO)

Herramientas:
Equipo de laboratorio
Liquido lava inyectores
Tinta especial
Bandeja de metal
P R O C E D I M I E N T O
1.- Desmontar el inyector del motor. Esto se consigue aflojando los tornillos del cuerpo de aceleración. En muchos casos suelen tener una traba, retire las trabas de a una. Estas trabas suelen estar colocadas en una ranura que tiene el cuello de cada inyector. Preste atención a la ranura. A veces algunos inyectores tienen dos ranuras y la traba. Siempre va colocada en la ranura superior. La Flecha indica la ranura donde va colocada la traba de sujeción La Flecha indica la ranura donde va colocada la traba de sujeción
2.- Una vez desmontado el inyector, límpielo primeramente por fuera, use para esto cualquier desengranaste o un poco de gasolina. Esto evitara que Ud. mismo ensucie el liquido en el equipo de ultrasonido
3.- Coloque el inyector en el equipo de ultrasonido y simultáneamente conecte el generador de pulsos. Ponga en funcionamiento el equipo de ultrasonido
4.- Deje funcionando el equipo de ultrasonido por unos 15 minutos, luego de este tiempo saque el inyector del liquido y sopleteelos ingresando el aire comprimido por la boca de acceso del combustible a los inyector. Para que el aire pase por dentro de los inyector, el generador debe estar funcionando
5.- Repita el procedimiento nuevamente. Desde el punto 3
6.- Lubricación interna del inyector. Cambio o lubricación de O rings de inyector.
7.-. Balance, calibración de inyectores. Control, revisión, limpieza y puesta a punto del sistema de inyección. Evaluación completa del sistema de inyección. Diagnóstico, revisión y control de la presión de combustible.
8.- Se colocan nuevamente asegurándose de que esté bien fijo el riel y se echa a andar para observar de que no exista falla.
RECURSOS
PARA EL DESARROLLO DEL PROYECTO "SISTEMA DE INYECCION DE COMBUSTIBLE T.B.I."
- MATERIALES
1. PC (computadora)
2. Memoria USB
3. CD (disco compacto)
- BIBLIOGRAFICOS
1. Libro: GM 1995, INYECCION DE COMBUSTIBLE, GM, MEXICO DF.
2. PAGINAS WEB
http://automecanico.com/
http://www.autoelectronico.com/
http://www.todomecanica.com/
http://www.mecanicavirtual.org/
http://www.mimecanicapopular.com/
http://autorepair.about.com/
http://www.autocity.com/
http://www.bloghella.com.mx/
- INSUMOS
1. Hrs. de Internet 15=$120
2. Impresiones 32 = $32
3. CD 2 = $12
4. Copias 14= $7
TOTAL= $171.00
CONLUSIONES
Se sabe, que la combustión en un motor es lo que determina el tiempo de vida de éste; así como la vida de todos los que habitamos este planeta, o sea que si la combustión permite la expulsión de gases altamente contaminantes, estaríamos dañando a nuestro planeta en forma muy veloz.Por esta razón tanto un carburador como el sistema TBI; funcionan sobre la base de una mezcla precisa de aire y combustible (14,7 partes de aire por 1 de combustible).
El carburador permite el ajuste manual de esta mezcla por lo cual un dispositivo mal regulado podría ser altamente nocivo. Dentro de la tolerancia 12 a 1 (mezcla rica en combustible); o 16 a 1 (mezcla pobre en combustible), es posible obtener diferentes resultados. Si se ajusta a una mezcla muy rica se pueden dañar las válvulas y pistones; y si se ajusta a muy pobre el motor pierde fuerza.Si la mezcla no es la correcta, tenemos una de las causas de un motor "desafinado" con lo cual el motor estaría sufriendo daños, y/o contaminando el medio ambiente.
El sistema TBI, en base a un monitoreo constante de sensores colocados en diferentes partes del motor, ajusta la mezcla, obedeciendo a un programa de su computadora de a bordo de tal manera que la entrega de la mezcla aire-combustible siempre sea la correcta.Pero cabe mencionar que un sistema de inyección TBI no es un eficiente al 100% en cuanto a la inyección, es por eso que en el transcurso de los años las compañías automotrices desarrollan sistema aun mas tecnológicos “en toda la extensión de la palabra” para la sociedad.
Publicado por alex9 en 11:50 No hay comentarios:
Introducción
En esta ocasión, hablaremos del sistema de inyección electrónica y de sus principales componentes.
Retomando un poco el tema de la introducción de este sistema, representó una ventaja abismal respecto al sistema del carburador tradicional por su "simplicidad" y eficiencia.
Simplicidad porque en aquella época los carburadores eran muy complicados pues se diseñaban para que cumplieran diferentes funciones de manera mecánica.
Eficiente pues, con la aparición de las medidas ambientales y la incorporación de los catalizadores y los sensores de Oxígeno a los sistemas de escape, sólo un sistema electrónico podía, en tiempo real, generar los ajustes en la inyección de gasolina que se requerían para el adecuado funcionamiento de los catalizadores, ya que estos estaban (y siguen estando) diseñados para "filtrar" cierta cantidad de contaminantes.

Este fue el paso intermedio desde el carburador y hacia la inyección electrónica moderna.
Con el desarrollo de nuevos motores, el sistema TBI evolucionó a un sistema que incorporaba un inyector por cada cilindro. Éste se denominó Multipunto o MPFI (Multi Port Fuel Injection, por sus siglas en inglés).
A diferencia del sistema TBI, este nuevo sistema ofrecía una dosificación mucho más precisa y con mucho menos desperdicio de combustible, pues cada inyector se localizaba en el múltiple de admisión orientando su descarga hacia la/las válvulas de admisión de cada cilindro.
Dichas mejoras acarrearon otros beneficios como la reducción en el consumo de combustible y una mejor eficiencia en la entrega de potencia.
A diferencia del sistema TBI, este nuevo sistema ofrecía una dosificación mucho más precisa y con mucho menos desperdicio de combustible, pues cada inyector se localizaba en el múltiple de admisión orientando su descarga hacia la/las válvulas de admisión de cada cilindro.
Dichas mejoras acarrearon otros beneficios como la reducción en el consumo de combustible y una mejor eficiencia en la entrega de potencia.

T B I: Throttle Body Injection ó CFI: Central Fuel Injection
Se conoce como T B I al Sistema de inyección que utiliza 1 o 2 inyectores eléctricos), colocados en la parte superior del sistema colector de combustible (de ahora en más lo llamaremos manifold de admisión o simplemente manifold).Este sistema se asemeja en figura a un carburador común y corriente tal como puede observarse en las figuras 1 y 3.Este sistema funciona valiéndose de una computadora instalada dentro del vehiculo. En cuanto se abre el switch (en cuanto se activa la llave de encendido) los inyectores reciben 12V en el borne positivo mientras que el borne negativo del inyector es controlado por la computadora, la cual se vale de un monitoreo constante de sus sensores instalados en diferentes partes del motor para evaluar su compartimiento, para ajustar la entrega de combustible, tratando siempre de mantener una mezcla perfecta de aire y gasolina (14,7 partes de aire por 1 de nafta).Es te sistema es utilizado por diferentes fabricantes de automóviles, especialmente los americanos. Sin embargo, cada fabricante emplea un sistema diferente de sensores y programas que corren en una computadora para definir el paso del combustible lo cual hace algo difícil uniformar los síntomas para diagnosticar las fallas que pueden producirse en un sistema de inyección electrónica. Sin embargo, a lo largo de diferentes artículos trataremos de hacer ajustes a nuestro criterio de diagnóstico para que usted se ubique en los síntomas particulares de su vehiculo.General Motors denomina TBI al uso de 1 o 2 inyectores colocados en la posición que se muestra en la fotografía de la figura 3. En la misma posición "Ford" denomina al sistema "Central Fuel Injection". Comprenderán que resulta ocioso estar denominando los sistemas de acuerdo con el criterio del fabricante.


Cómo funciona el sistemaTBI
El sistema de inyección electrónica utilizado actualmente en los motores de los automóviles es mucho mejor que el antiguo sistema que utilizaba carburadores.Además, una de las principales características de los sistemas de inyección electrónica de combustible en los automóviles modernos, es el monitoreo del estado del motor que se lleva a cabo a través de una serie de sensores ubicados estratégicamente. Cabe mencionar que dicha vigilancia tiene como principal objetivo, ajustar la mezcla aire-combustible para lograr una inyección ideal, tanto en tiempo como en proporciones óptimas.
El sistema de inyección electrónica utilizado actualmente en los motores de los automóviles es mucho mejor que el antiguo sistema que utilizaba carburadores.Además, una de las principales características de los sistemas de inyección electrónica de combustible en los automóviles modernos, es el monitoreo del estado del motor que se lleva a cabo a través de una serie de sensores ubicados estratégicamente. Cabe mencionar que dicha vigilancia tiene como principal objetivo, ajustar la mezcla aire-combustible para lograr una inyección ideal, tanto en tiempo como en proporciones óptimas.
Componentes del sistema de inyección TBIActuador de ralentí
Es el encargado de mantener el numero de revoluciones de ralentí bajo las condiciones del motor en marcha mínima.

Acumulador de combustible.El acumulador de combustible mantiene bajo presión durante un tiempo al sistema después de parar el motor, asegurando el arranque perfecto con el motor caliente.

Sensor de mariposa
Este interruptor esta montado encima de la mariposa. Es el encargado de enviar la señal de la posición del acelerador.
Este interruptor esta montado encima de la mariposa. Es el encargado de enviar la señal de la posición del acelerador.

Sensor de temperaturaEl interruptor térmico limita el tiempo de inyección de la válvula de arranque en frio, hasta que el motor alcanza una temperatura normal.

Inyectores
Estas válvulas abren a una señal definida y son los encargados de suministrar el combustible.

Estas válvulas abren a una señal definida y son los encargados de suministrar el combustible.

Amortiguador de presión.
El amortiguador de presión suaviza las puntas de presión para reducir ruidos.
El amortiguador de presión suaviza las puntas de presión para reducir ruidos.

Bomba de combustibleLa bomba de combustible suministra en forma continua el combustible al sistema. La presión de la bomba siempre tiene que ser mayor que la demanda máxima de combustible del motor para mantener siempre la presión necesaria.

Líneas de alimentación y retorno de combustible
Son tuberías que conducen el combustible hacia los inyectores y que retorna en el tanque de combustible.

Limitadores de presión.El limitador de presión controla la diferencia de presiones antes y después de la mariposa del acelerador. En el caso de sobre pasar la diferencia de presión ajustada, circula aire adicional del tubo de aspiración.

Filtro de la bomba o cedazo
Filtra partículas de polvo o cualquier otra impureza que flota en el tanque de combustible.
Filtra partículas de polvo o cualquier otra impureza que flota en el tanque de combustible.

Medidor del caudal de aire
Es el encargado de medir a través de una aleta sonda gobernada por un resorte, la cantidad de aire que entra al motor.
Es el encargado de medir a través de una aleta sonda gobernada por un resorte, la cantidad de aire que entra al motor.

Filtro de combustibleSe encarga de filtra partículas provenientes del tanque de combustible.

Medidor de masa de aire.Es el encargado de medir la masa de aire que entra en el sistema por medio de un hilo caliente.

Potenciómetro de la mariposa.El potenciómetro de la mariposa está montado sobre la unidad central de inyección .este elemento registra la posición del acelerador y la velocidad del Angulo de los movimientos de apertura y cierre.

Regulador de presión.
Los reguladores de presión son los encargados de mantener constante presión dentro del tubo de alimentación de combustible.

Relevador de la bomba.
Tiene la función de conmutar; es decir, hace que el circuito de alimentación de la bomba pase de la condición de cerrado a la conducción de abierto.
Tiene la función de conmutar; es decir, hace que el circuito de alimentación de la bomba pase de la condición de cerrado a la conducción de abierto.

Sensor de presiónLos sensores de presión registran la presión y la transmiten como señal eléctrica a la unidad de mando.

Sondas lambda o sensores de oxigeno.Mide el contenido de oxigeno de los gases de escape enviando una señal eléctrica a la unidad de control electrónico.

Sondas térmicas.Mide la temperatura del motor y entrega una señal eléctrica a la unidad de control electrónico.


Cuerpo de aceleración.
Esta unidad controla y coordina a la válvula de inyección, el regulador de presión, la mariposa y el actuador de mariposa así como los sensores de temperatura de aire y de la posición de la mariposa.
Esta unidad controla y coordina a la válvula de inyección, el regulador de presión, la mariposa y el actuador de mariposa así como los sensores de temperatura de aire y de la posición de la mariposa.

Tanque de combustible.Es un dispositivo en el cual se guarda el combustible.

Unidad de control electrónicoDetermina la presión y cantidad de combustible necesaria de combustible y controla todos los elementos de ajuste y las válvulas de inyección.


Presión de combustible

En la actualidad, existen reguladores electrónicos que monitorean la presión del combustible y le "avisan" a la ECU (computadora) cuándo aumentar o disminuir la misma. Para compensar esto, la ECU hace que aumente o disminuya dicha presión (según corresponda), mediante la activación o desactivación de la bomba de combustible.Al ser inyectada la gasolina con la presión adecuada en el cuerpo del acelerador, se inicia el proceso de combustión.Dependiendo del diseño del sistema de inyección, se prefiere modificar la presión para llevar a cabo una mejor atomización del combustible; esto evita que en la gasolina haya partículas más pequeñas; y con ello, se obtiene una combustión aceptable de la mezcla aire-gasolina.

Mantenimiento
Con el paso del tiempo y el uso de nuestro vehículo, los inyectores van perdiendo eficacia debido a la contaminación con depósitos de resinas, carbones y otras impurezas, especialmente en los vehículos de Inyección Electrónica convertidos a GNC, esta situación es aún más grave ya que los inyectores permanecen por gran tiempo sin pulverizar combustible.
Debido a esto se genera un aumento de temperatura con formación de lacas y barnices que van lentamente tapando los orificios de los inyectores, y como consecuencia tenemos un incremento en el consumo de combustible en un 10% aproximadamente, ya que la computadora de nuestro auto compensa esta deficiencia con mayores tiempos de inyección de combustible.

La Limpieza de Inyectores, normalmente es parte de un servicio de afinación, sin embargo, se puede realizar solamente este servicio para mejorar el funcionamiento del auto.
El sistema fuel injection está formado por; la bomba de combustible, líneas de gasolina, riel de inyectores, regulador de presión y líneas de retorno. Los inyectores actúan como diminutas llavecitas que suministran combustible en forma de spray, y mezclado con el aire y la chispa que producen las bujías se genera la combustión.No es una situación simple de manejar, es muy importante darle tiempo de mantenimiento a nuestro auto, los grandes problemas técnicos comienzan por pequeños descuidos o desidia de hacer las cosas, si es nuestro medio de transporte, ¿por qué no darnos el tiempo para preocuparnos por su mantenimiento?, y así poder viajar cómodos y seguros.

Los sistemas de inyección de combustible funcionan bajo presión. Típicamente, la gasolina es mantenida entre 2 a 3,5 kg/cm2 (35 a 50 libras/pulgada2) en un tanque montado en la bomba de combustible. En alguna parte en el conducto entre la bomba y los inyectores hay un filtro de combustible grande. Para garantizar que siempre haya suficiente combustible para todas las condiciones, conducto de retorno envía el exceso de combustible de regreso al tanque.
Cada inyector de combustible tiene en un extremo una válvula controlada por un solenoide. Un resorte mantiene la válvula asentada fuertemente contra el combustible contenido a presión dentro del inyector.
La computadora del motor envía una señal eléctrica al inyector, haciendo que el solenoide hale la válvula fuera de su asiento. A medida que la válvula, se abre, deja expuestos unos pequeños agujeros hechos de forma precisa en el extremo del inyector, llamado, orificios atomizadores, que permiten que el combustible sea atomizado.
A una orden de la computadora del motor, el solenoide libera la válvula, la que se cierra con la ayuda del resorte.La cantidad de combustible atomizado es regulado por la cantidad de tiempo que la válvula permanece abierta.
El solenoide la abre y cierra tan rápidamente, que el instante que está abierta se llama pulsación. El patrón del combustible atomizado es determinado por la forma y tamaño de los orificios y es exacto a la forma y tamaño de las aberturas de admisión. Los motores con dos válvulas de admisión por cilindro, tienen un inyector con un atomizador dividido, para inyectar la misma cantidad de combustible a ambas válvulas.
Carburación o inyección
El sistema de carburación, ha sido durante años el sistema por excelencia en los motores de gasolina. Se trata de un sistema mecánico que no requiere la gestión de una centralita, pues prepara la mezcla de aire-combustible en la propia admisión. Cuando entra el aire en la admisión y cruza el sistema de carburación, funciona del mismo modo que un pulverizador de pintura. Cuanto más aire entra, mayor es la fuerza que empuja el combustible. Es un sistema antiguo pero que, en el fondo, nunca falla. Aunque no es nada eficiente.
La carburación se vio superada por el sistema actual por excelencia, la inyección de combustible. Un sistema que inyecta el combustible directamente en la cámara de combustión, o en el caso de la mayoría de los diésel, en la precámara de combustión (ubicada en la culata).
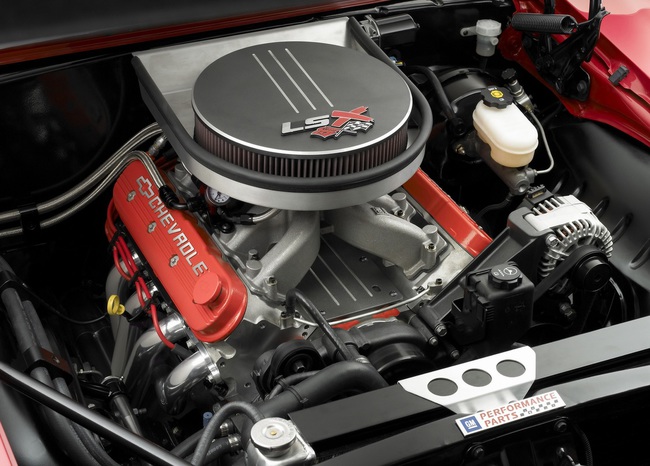
Ventajas de los sistemas de inyección
Consumo eficiente
A diferencia del sistema de carburación, los inyectores van regulados por la centralita normalmente (aunque veremos que hay otras formas). La ventaja es que en el motor, hay momentos en los que la entrada de aire no coincide con el flujo de gasolina. La carburación se regula mediante la presión del aire, pero a bajas revoluciones no es necesario tanto volumen de combustible. Si sumamos todas esos momentos en en los que se derrocha gasolina, el ahorro es considerable.
Mayor rendimiento
Otro de los problemas de la carburación, aunque sea reconocido como un sistema de competición es que, en el fondo, el rendimiento no es del todo bueno. Básicamente, la gasolina se introduce en los cilindros a chorro, es decir, no cubre toda la superficie por igual. La inyección permite cubrir todas las zonas de la cámara interna, donde van alojados los cilindros, consiguiendo así una explosión armónica. En definitiva, esto consigue aumentar el par motor.
Menos contaminación
Los gases que expulsan los motores de inyección son menos contaminantes. Al suministrarse la gasolina en proporciones adecuadas, los gases son más refinados y controlados. De ahí viene la típica expresión de “va rico en gasolina”. Si el lector tiene la oportunidad de ver un coche de carburación, los olores del escape a veces van algo cargados y es exactamente ese el principio por el que se rige dicho comentario.
Mejora el arranque y el calentamiento del motor
Por último, pero no menos importante, los motores de inyección logran incrementar antes la temperatura del motor gracias al correcto suministro de combustible. Los motores de carburación al distribuir desde el momento de arranque, grandes cantidades de gasolina, no consiguen un arranque rápido, pues no cubren bien todas las superficies desde el principio y, además, el ralentí es muy inestable. Y cuando un motor va a tirones, necesitará mucho tiempo para alcanzar su temperatura adecuada de funcionamiento.
Qué sistemas de inyección hay en el mercado
1. Ubicación de los inyectores
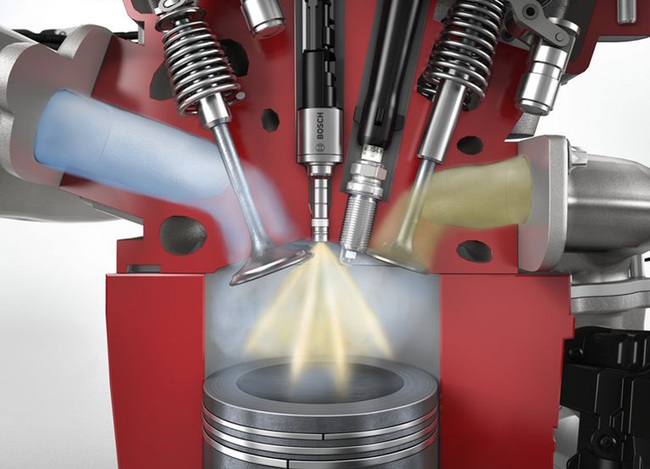
Inyección directa
Este sistema inyecta directamente el combustible en la cámara de combustión. Generalmente, estos inyectores van ubicados en la parte más próxima al bloque del motor, en la zona final de los colectores de admisión. De esta forma entra directamente en la cámara del bloque y es ahí, donde se mezcla la gasolina con el aire. Hoy en día, es el método más usado.
Inyección indirecta
Este sistema ubica los inyectores (no suelen ser más de dos) en el propio colector de admisión. Es importante no confundirlo con el sistema de carburación que, aunque también va alojado en la admisión, no incorpora ningún inyector. Por tanto, el inyector actúa en contacto directo con el aire y entra al bloque en forma de mezcla. Este tipo de sistemas no se usa demasiado en la actualidad, aunque si lo incorporan losmotores de baja cilindrada como por ejemplo en el Peugeot 108.
2. Número de inyectores
Este apartado va estrechamente relacionado con la ubicación de inyectores, pero muestra alguna diferencia.
Inyección monopunto
La inyección monopunto, hace referencia a los sistemas que utilizan un solo inyector. Obviamente, siempre va ubicado en el colector de admisión, pues no puede inyectar directamente en la cámara, porque se necesitaría un inyector por cada cilindro. En resumen, es un sistema de inyección indirecta como el que acabamos de explicar.
Inyección multipunto
En este caso, la inyección multipunto tiene tantos inyectores como cilindros. La gran diferencia, reside en que la inyección del combustible puede ser tanto directa como indirecta. Pudiéndose ubicar en la parte final de colector de admisión, para que el flujo vaya directo a la cámara del motor, o colocarse en los colectores de admisión en una zona próxima, en la que se mezcle con el aire antes de entrar en la zona interior donde están los cilindros. Este sistema lo incorporan la mayoría de los vehículos de gama media y alta. Se trata de la opción de inyección directa la más popular.
3. Según las veces que inyecten
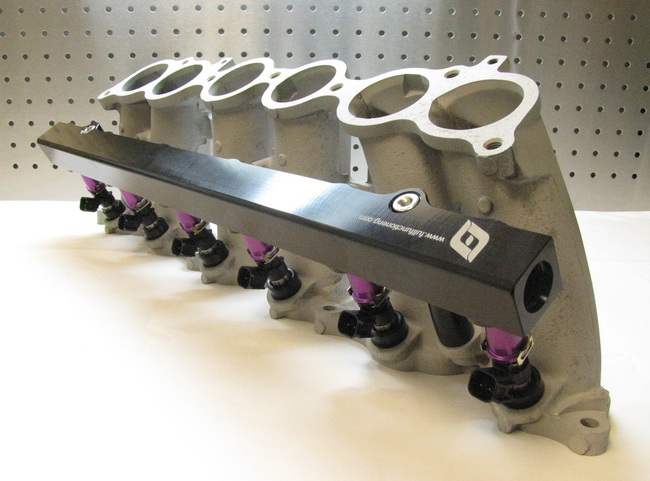
Inyección continua
Como su propio nombre indica, el suministro de combustible se hace sin pausas Solamente se regula el flujo, pero la inyección es constante. Es decir, aunque esté a ralentí el motor, se inyecta una pequeña dosis de combustible.
Inyección intermitente
Este sistema es totalmente electrónico. Funciona en base a las órdenes de la centralita. Los inyectores trabajan de forma intermitente pero, a diferencia de la inyección continua, puede parar de suministrar en caso de que el motor no lo requiera. Es el sistema más usado y, a su vez, se divide en tres tipos:
1. Secuencial
La inyección intermitente secuencial, inyecta combustible a cada cilindro por separado, mediante un control exhaustivo por parte de la centralita, apelando así a la pura eficiencia.
2. Semisecuencial
Al igual que la inyección secuencial, la semisecuencial sigue el mismo principio, pero en este caso se hacede dos en dos. Es decir, es un motor de cuatro cilindros, suministra el combustible primero a los cilindros uno y dos, seguido de una inyección en los cilindros tres y cuatro (las combinaciones pueden ser variadas).
3. Simultánea
Este último sistema intermitente, es usado en los motores más potentes por norma general. Utilizando las ventajas del sistema intermitente, en este caso, la inyección se realiza sobre todos los cilindros al mismo tiempo. No se separan, sino que cuando la centralita da la orden de que el motor necesita combustible, estos simplemente esparcen el flujo por todos los cilindros.
4. Mecanismos de inyección
Sistema de inyección mecánica
El sistema de inyección mecánico, apareció en 1932 para motores de la aviación, pero no llegaron a los vehículos hasta el año 1945. Un sistema que carece de electrónica al igual que el carburador. Los inyectores trabajan mediante la presión sometida por parte de un dosificador, una especie de distribuidor que reparte la gasolina por los inyectores que distribuyen la gasolina de forma simultánea, determinado por el caudalímetro.
Hoy en día no se suele utilizar, ya que no es tan eficiente como un sistema electrónico.
Sistemas de inyección electrónica
El primer sistema de inyección electrónica se comercializó en 1967, con el D-Jetroninc de Bosch. A lo largo de los años, este lanzamiento supuso la culminación de los sistemas de inyección. Se han seguido desarrollando hasta conseguir la más pura eficiencia. A diferencia de los sistemas KE-Jetronic, un híbrido entre un sistema mecánico y eléctrico, este aprovecha la tecnología al máximo para distribuir correctamente en combustible en el momento adecuado. Es por ello que los sistemas de la actualidad se basan en este sistema.


INYECCIÓN DIRECTA
Consiste en inyectar el combustible directamente en la cámara de combustión sobre la cabeza del pistón. Este sistema se empleaba habitualmente en vehículos pesados, ya que proporciona un excelente para motor y una gran economía de combustible, en su contra tienen el incoveniente de ser motores poco revolucionados y lentos de giro, y además producen mucho ruido en su funcionamiento. En la actualidad, estos incovenientes se están minimizando gracias a la aparición de la gestión electrónica diesel.
En este caso, la cámara de combustión está ubicada justo encima del pistón, el cual a su vez dispone de una cavidad en la cabeza donde se produce la combustión.
Dicha cavidad se perfecciona con relación a su diámetro, profundidad, conicidad del fondo y anillo de turbulencia para producir una combustión lo más acertada posible.
Los colectores de admisión se diseñan para producir una turbulencia a la entrada del cilindro y provocar un torbellino acelerado por la compresión del pistón. El inyector se encuentra ubicado en el centro de la cámara de combustión sobre el hueco de la cabeza del pistón y está constituido por una serie de orificios, normalmente cinco.
Estos se encuentran distribuidos uniformemente a su alrededor e inclinados hacia la cavidad de la cabeza del pistón. La colocación de los orificios del inyector con el hueco de la cabeza del pistón es un factor determinante en la instalación del inyector en forma de lápiz.
En un motor de inyección directa la combustión se realiza en un tiempo más reducido que en uno de cámara auxiliar, por lo que resulta una combustión más violenta. El aumento en el nivel de ruido producido en la combustión, de modo particular durante la aceleración, se ve gratificado por ahorro de carburante de hasta un 20%, representando una gran economía en este tipo de vehículos

SISTEMA DE ALIMENTACION DIESEL

Pag 07-26
SOBREALIMENTACION DE MOTORES DIESEL
La sobrealimentación consigue aumentar el par motor y la potencia del vehículo sin variar la cilindrada ni el régimen del motor, elevando el valor de la presión media efectiva del cilindro del motor.Un motor sobrealimentado puede conseguir hasta un 40% más de potencia que un motor de iguales características no sobrealimentado. Este aumento de potencia se debe tener en cuenta a la hora de fabricar los motores con el objetivo de evitar sobrecalentamientos del motor o presiones y temperaturas excesivas de encendido en la cámara de combustión provocados por la alta capacidad de entrega de aire y presión. De todas formas,se emplean dispositivos que limitan la velocidad máxima o rendimiento de potencia para evitar perjudicar al motor.
El turbocompresor
El turbocompresor es una bomba de aire diseñada para operar con la energía que normalmente se pierde en los gases de escape del motor.
Estos gases impulsan la rueda de turbina (lado escape) que va acoplada a la rueda de compresor (lado Admisión). Cuando giran, aportan un gran volumen de aire a presión, aumentando la presión en las cámaras de combustión del motor.
El turbocompresor es el más utilizado porque no consume potencia del
motor y puede girar a más de 100 000 rpm. Se pueden clasificar en :
– Turbocompresores de geometría fija.
– Turbocompresores de geometría variable.
El turbocompresor es una bomba de aire diseñada para operar con la energía que normalmente se pierde en los gases de escape del motor.
Estos gases impulsan la rueda de turbina (lado escape) que va acoplada a la rueda de compresor (lado Admisión). Cuando giran, aportan un gran volumen de aire a presión, aumentando la presión en las cámaras de combustión del motor.
El turbocompresor es el más utilizado porque no consume potencia del
motor y puede girar a más de 100 000 rpm. Se pueden clasificar en :
– Turbocompresores de geometría fija.
– Turbocompresores de geometría variable.
La energía térmica, de velocidad y presión de los gases de escape del motor son utilizadas para hacer girar el rotor de la turbina. La velocidad de rotación del conjunto rotativo y rotor del compresor es determinada por la forma y tamaño del rotor y la carcaza de la turbina. La carcaza actúa como un caracol, dirigiendo el flujo del gas para los álabes del rotor de la turbina, éstos giran con las misma rotación. El aire filtrado es aspirado por el rotor y la carcaza del compresor, donde es comprimido y distribuido a través del colector de admisión para la cámara de combustión.




Sistema intercooler
El sistema intercooler consiste en un intercambiador de calor en el que se introduce el aire que sale del turbocompresor para enfriarlo antes de introducirlo en los cilindros del motor.
Al enfriar el aire disminuye la densidad de éste por lo que para el mismo volumen de los cilindros se puede introducir mayor masa de aire y así mejorar el rendimiento del motor.
Inyeccion electronica diesel
Dentro de los motores de inyección directa hay que distinguir tres sistemas diferentes a la hora de inyectar el combustible dentro de los cilindros.
- Mediante bomba de inyección rotativa.
- Common Rail.
- Inyector-bomba.

Diferentes sistemas:
1.- Sistema que utiliza la tecnología tradicional de los motores diesel de "inyección indirecta" basado en una bomba rotativa (por ejemplo la bomba "tipo VE" de BOSCH) que dosifica y distribuye el combustible a cada uno de los cilindros del motor. Esta bomba se adapta a la gestión electrónica sustituyendo las partes mecánicas que controlan la "dosificación de combustible" así como la "variación de avance a la inyección" por unos elementos electrónicos que van a permitir un control mas preciso de la bomba que se traduce en una mayor potencia del motor con un menor consumo. Este sistema es utilizado por los motores TDI del grupo Volkswagen y los DTI de Opel y de Renault, así como los TDdi de FORD.

Foto de una bomba de inyección rotativa (bomba electrónica con su centralita).
3.- Sistema de Bomba-inyector en el que se integra la bomba y el inyector en el mismo cuerpo con eso se consigue alcanzar presiones de inyección muy altas (2000 Bares), con lo que se consigue una mayor eficacia y rendimiento del motor.. Existe una bomba-inyector por cada cilindro. Este sistema es utilizado por el grupo Volkswagen en sus motores TDI de segunda generación.

En la figura de arriba tenemos todos los componentes que forman un sistema de alimentación para motores TDi
de ultima generación que utilizan la nueva tecnología de la bomba-inyector.
1.- Sistema que utiliza la tecnología tradicional de los motores diesel de "inyección indirecta" basado en una bomba rotativa (por ejemplo la bomba "tipo VE" de BOSCH) que dosifica y distribuye el combustible a cada uno de los cilindros del motor. Esta bomba se adapta a la gestión electrónica sustituyendo las partes mecánicas que controlan la "dosificación de combustible" así como la "variación de avance a la inyección" por unos elementos electrónicos que van a permitir un control mas preciso de la bomba que se traduce en una mayor potencia del motor con un menor consumo. Este sistema es utilizado por los motores TDI del grupo Volkswagen y los DTI de Opel y de Renault, así como los TDdi de FORD.

Foto de una bomba de inyección rotativa (bomba electrónica con su centralita).
2.- Sistema de conducto común (common-rail) en el que una bomba muy distinta a la utilizada en el sistema anterior, suministra gasoleo a muy alta presión a un conducto común o acumulador donde están unidos todos los inyectores. En el momento preciso una centralita electrónica dará la orden para que los inyectores se abran suministrando combustible a los cilindros. Esta tecnología es muy parecida a la utilizada en los motores de inyección de gasolina con la diferencia de que la presión en el conducto común o acumulador es mucho mayor en los motores diesel (1300 Bares) que en los motores gasolina (6 Bares máximo).
Este sistema es utilizado por los motores, DCI de Renault de nueva generación, los HDI del Grupo PSA y los JTD del Grupo Fiat,
Este sistema es utilizado por los motores, DCI de Renault de nueva generación, los HDI del Grupo PSA y los JTD del Grupo Fiat,


En la figura de arriba tenemos todos los componentes que forman un sistema de alimentación para motores TDi
de ultima generación que utilizan la nueva tecnología de la bomba-inyector.
Inyección electrónica diesel
Llamada en ingles EDC (Electronic Diesel Control). La inyección electrónica diesel es propiamente un sistema de gestión del motor capaz de monitorear y controlar todas la variables y sistemas involucradas en la entrega del combustible diesel a los cilindros bajo cualquier condición de operación con la finalidad de que dicha entrega de combustible se de en la cantidad exacta y en el momento preciso y con el mínimo de emisiones contaminantes.
De forma general, el sistema de gestión electrónica tiene sensores que miden en cada intervalo de tiempo las rpm y temperatura del motor, la presión y temperatura del aire en el múltiple de admisión, la posición del árbol de levas, y la posición del acelerador entre otras variables.
De forma general, el sistema de gestión electrónica tiene sensores que miden en cada intervalo de tiempo las rpm y temperatura del motor, la presión y temperatura del aire en el múltiple de admisión, la posición del árbol de levas, y la posición del acelerador entre otras variables.
Estas señales son enviadas al CPU (Central Process Unit), donde son digitalizadas, de este modo pueden ser manipuladas y procesadas en intervalos de tiempo muy pequeños el resultado es una orden emitida a los actuadores electromecánicos encargados de inyectar el combustible, y/o controlar el adelanto o atraso de la inyección. Los sistemas EDC pueden operar tanto en lazo abierto como cerrado. Ver figuras.
El EDC es aplicable a todos los sistemas de inyección diesel modernos, esto es:
El EDC es aplicable a todos los sistemas de inyección diesel modernos, esto es:
Aunque estos sistemas de inyección difieren en muchos aspectos, y están instalados en una amplia variedad de diferentes vehículos, todos ellos están equipados con una forma similar de EDC.

gestion de la inyeccion electronica diesel
Circuito neumático de frenos de un camión.
1) Compresor. 2) Regulador de presión. 3) Secador de aire. 4) Depósito de regeneración. 5) Válvula de protección de cuatro vías. 6) Depósitos de aire comprimido. 7) Válvula defreno de mano. 8) Válvula de descarga del freno de mano. 9) Válvula de freno de servicio. 10) Cámaras de aire de frenos delanteros. 11) Válvula de control del reparto de frenada. 12) Cámaras de aire de frenos traseros.
COMPRESOR DE AIRE.
Una bomba de émbolo, denominada también compresor de aire, origina la presión necesaria para el sistema de frenos de aire comprimido. El compresor tiene uno o dos émbolos, y es accionado el mismo motor del vehículo, por medio de una banda de transmisión. Se lo denomina también de simple efecto ya que aspira directamente el aire de la atmósfera.
La lubricación se realiza por medio del aceite del motor a través de un tubo de entrada al carter del mismo que engrasa el cigüeñal y cabeza de biela a presión, siendo el resto de los elementos lubricados por barboteo, retornando el aceite al carter del compresor que sale al motor a través de la tapa de distribución.
SISTEMA DE FRENO DE AIRE COMPRIMIDO
1. INTRODUCCIÓN.
La razón de utilizar el aire comprimido es por su versatilidad y su rapidez de respuesta en el trabajo. Su acción no es tan inmediata como la eléctrica, pero sí es notablemente más rápida que la hidráulica. Hemos de pensar que la neumática se sirve, como materia prima, del aire atmosférico que nos circunda, el cual podemos tomarlo en la cantidad que sea necesario para comprimirlo y transformar su energía
en trabajo.
La compresión se hace en un central de compresor, el aire comprimido es fácilmente transportable, aún en largas distancias, por medio de tuberías, las cuales distribuyen la presión de trabajo uniforme hacia los puestos o lugares de consumo.
Por ser el aire un fluido compresible, podemos almacenarlo fácilmente en depósitos,los cuales sirven, además, para regular la entrada en funcionamiento del compresor.

1) Compresor. 2) Regulador de presión. 3) Secador de aire. 4) Depósito de regeneración. 5) Válvula de protección de cuatro vías. 6) Depósitos de aire comprimido. 7) Válvula defreno de mano. 8) Válvula de descarga del freno de mano. 9) Válvula de freno de servicio. 10) Cámaras de aire de frenos delanteros. 11) Válvula de control del reparto de frenada. 12) Cámaras de aire de frenos traseros.
COMPRESOR DE AIRE.
Una bomba de émbolo, denominada también compresor de aire, origina la presión necesaria para el sistema de frenos de aire comprimido. El compresor tiene uno o dos émbolos, y es accionado el mismo motor del vehículo, por medio de una banda de transmisión. Se lo denomina también de simple efecto ya que aspira directamente el aire de la atmósfera.
La lubricación se realiza por medio del aceite del motor a través de un tubo de entrada al carter del mismo que engrasa el cigüeñal y cabeza de biela a presión, siendo el resto de los elementos lubricados por barboteo, retornando el aceite al carter del compresor que sale al motor a través de la tapa de distribución.
Inyección gasolina (continuación...)
|
El sistema K-Jetronic de Bosch proporciona un caudal variable de carburante pilotado mecánicamente y en modo continuo. Este sistema realiza tres funciones fundamentales:
- Medir el volumen de aire aspirado por el motor, mediante un caudalímetro especial.
- Alimentación de gasolina mediante una bomba eléctrica que envía la gasolina hacia un dosificador-distribuidor que proporciona combustible a los inyectores.
- Preparación de la mezcla: el volumen de aire aspirado por el motor en función de la posición de la válvula de mariposa constituye el principio de dosificación de carburante. El volumen de aire esta determinado por el caudalímetro que actúa sobre el dosificador-distribuidor.
Componentes del modelo K-jetronic
Alimentación de combustibleEl sistema de alimentación suministra bajo presión la cantidad exacta de combustible necesaria para el motor en cada estado de funcionamiento. El sistema de alimentación consta del depósito de combustible (1), la electrobomba de combustible (2), el acumulador de combustible (3), el filtro de combustible (4), el regulador de presión (5), el distribuidor-dosificador de combustible (16) y las válvulas de inyección (9). Una bomba celular de rodillos accionada eléctricamente aspira el combustible desde el depósito y lo conduce bajo presión a través de un acumulador de presión y un filtro.
Bomba eléctrica de combustible: Es una bomba de tipo centrifugo situado a la salida del deposito; en un interior hay una cámara excéntrica con un disco que contiene cinco cavidades donde están los rodillos. Debido a la fuerza centrifuga los rodillos resultan proyectados contra las paredes, aumentando el volumen de las cavidades y aspirando la gasolina, que se impulsa hasta el tubo distribuidor.
La bomba tiene una válvula de descarga que limita la presión del circuito. De esta manera se evita que una posible obstrucción provoque la avería de la propia bomba.
Cuando la bomba esta parada, una válvula a la salida mantiene una presión residual en el circuito.
El motor de la bomba esta bañado en la propia gasolina que le sirve al mismo tiempo de lubrificante y refrigerante.
Aunque pueda parecer que existe riesgo de inflamación el estar en contacto con la gasolina con el motor eléctrico, esto no es posible debido a la ausencia de aire para la combustión.
Al poner el contacto del vehículo la bomba se pone en marcha permaneciendo en funcionamiento todo el tiempo en que el motor esta en marcha.
Un sistema de seguridad detiene la bomba cuando no hay mando de encendido.
La bomba tiene una válvula de descarga que limita la presión del circuito. De esta manera se evita que una posible obstrucción provoque la avería de la propia bomba.
Cuando la bomba esta parada, una válvula a la salida mantiene una presión residual en el circuito.
El motor de la bomba esta bañado en la propia gasolina que le sirve al mismo tiempo de lubrificante y refrigerante.
Aunque pueda parecer que existe riesgo de inflamación el estar en contacto con la gasolina con el motor eléctrico, esto no es posible debido a la ausencia de aire para la combustión.
Al poner el contacto del vehículo la bomba se pone en marcha permaneciendo en funcionamiento todo el tiempo en que el motor esta en marcha.
Un sistema de seguridad detiene la bomba cuando no hay mando de encendido.
Acumulador de combustible: mantiene bajo presión el circuito de carburante después del paro del motor, para facilitar una nueva puesta en marcha, sobretodo si el motor esta caliente.
Gracias a la forma particular de su cuerpo, el acumulador ejerce una acción de amortiguación de los impulsos presentes en el circuito y debidos a la acción de la bomba.
El interior del acumulador esta dividido por dos cámaras separadas por una membrana (4). Una cámara (5) tiene la misión de acumular carburante y la otra (1) contiene un muelle.
Durante el funcionamiento, la cámara de acumulación se llena de carburante y la curva se curva hasta el tope, oponiendose a la presión ejercida por el muelle. La membrana queda en esta posición, que corresponde al volumen máximo hasta que el motor deja de funcionar. A medida que el circuito de carburante va perdiendo presión la membrana va desplazandose para compensar esta falta de carburante.
Gracias a la forma particular de su cuerpo, el acumulador ejerce una acción de amortiguación de los impulsos presentes en el circuito y debidos a la acción de la bomba.
El interior del acumulador esta dividido por dos cámaras separadas por una membrana (4). Una cámara (5) tiene la misión de acumular carburante y la otra (1) contiene un muelle.
Durante el funcionamiento, la cámara de acumulación se llena de carburante y la curva se curva hasta el tope, oponiendose a la presión ejercida por el muelle. La membrana queda en esta posición, que corresponde al volumen máximo hasta que el motor deja de funcionar. A medida que el circuito de carburante va perdiendo presión la membrana va desplazandose para compensar esta falta de carburante.
Medición del caudal de aire
El regulador de mezcla cumple dos funciones medir el volumen de aire aspirado por el motor y dosificar la cantidad correspondiente de combustible para conseguir una proporción aire/combustible adecuada. El medidor del caudal de aire), situado delante de la mariposa en el sistema de admisión mide el caudal de aire. Consta de un embudo de aire (2) con un plato-sonda móvil colocado en el nivel de diámetro más pequeño. Cuando el motor aspira el aire a través dei embudo, el plato (1) es aspirado hacía arriba o hacia abajo (depende de cada instalación), y abandona su posición de reposo. Un sistema de palancas transmite el movimiento del plato a la válvula corredera (8) que determina la cantidad de combustible a inyectar. Al parar el motor el plato-sonda vuelve a la posición neutra y descansa en un resorte (3) de lámina ajustable (en el caso de los platos-sonda que se desplazan hacia arriba). Para evitar estropear la sonda en caso de retornos de llama por el colector de admisión, el plato-sonda puede oscilar en el sentido contrario, contra el resorte de lámina, hacia una sección más grande. Un amortiguador de goma limita su carrera.
El regulador de mezcla cumple dos funciones medir el volumen de aire aspirado por el motor y dosificar la cantidad correspondiente de combustible para conseguir una proporción aire/combustible adecuada. El medidor del caudal de aire), situado delante de la mariposa en el sistema de admisión mide el caudal de aire. Consta de un embudo de aire (2) con un plato-sonda móvil colocado en el nivel de diámetro más pequeño. Cuando el motor aspira el aire a través dei embudo, el plato (1) es aspirado hacía arriba o hacia abajo (depende de cada instalación), y abandona su posición de reposo. Un sistema de palancas transmite el movimiento del plato a la válvula corredera (8) que determina la cantidad de combustible a inyectar. Al parar el motor el plato-sonda vuelve a la posición neutra y descansa en un resorte (3) de lámina ajustable (en el caso de los platos-sonda que se desplazan hacia arriba). Para evitar estropear la sonda en caso de retornos de llama por el colector de admisión, el plato-sonda puede oscilar en el sentido contrario, contra el resorte de lámina, hacia una sección más grande. Un amortiguador de goma limita su carrera.
Para la adaptación de la relación aire/combustible a diferentes regímenes del motor: ralentí, carga parcial y plena carga, el embudo del caudalímetro esta compuesto de secciones que presentan diferentes pendientes. En las zonas de ralentí y plena carga la pendiente del embudo permitirá que el plato sonda se eleve mas para así poder enriquecer mas la mezcla.
Admisión de combustible
El dosificador-distribuidor de combustible dosifica la cantidad necesaria de combustible y la distribuye a los inyectores. La cantidad de combustible varia en función de la posición del plato-sonda del medidor del caudal de aire, y por lo tanto en función del aire aspirado por el motor. Un juego de palancas traduce la posición del plato-sonda en una posición correspondiente a la válvula de corredera. La posición de la válvula corredera en la cámara cilíndrica de lumbreras determina la cantidad de combustible a inyectar. Cuando el émbolo se levanta, aumenta la sección liberada en las lumbreras, dejando así pasar más combustible hacia las válvulas de presión diferencial (cámaras superiores) y de estas hacia los inyectores. Al movimiento hacia arriba del émbolo de control se opone la fuerza que proviene del circuito de presión de mando. Esta presión de mando está regulada por el "regulador de la presión de mando" y sirve para asegurar que el émbolo de la válvula corredera sigue siempre inmediatamente el movimiento del plato-sonda sin que permanezca en posición alta cuando el plato-sonda vuelve a la posición de ralentí. Las válvulas de presión diferencial del dosificador-distribuidor de combustible aseguran el mantenimiento de una caída de presión constante entre los lados de entrada y de salida de las lumbreras. Esto significa que cualquier variación en la presión de línea del combustible o cualquier diferencia en la presión de apertura entre las inyectores no puede afectar el control del caudal de combustible.
El dosificador-distribuidor de combustible dosifica la cantidad necesaria de combustible y la distribuye a los inyectores. La cantidad de combustible varia en función de la posición del plato-sonda del medidor del caudal de aire, y por lo tanto en función del aire aspirado por el motor. Un juego de palancas traduce la posición del plato-sonda en una posición correspondiente a la válvula de corredera. La posición de la válvula corredera en la cámara cilíndrica de lumbreras determina la cantidad de combustible a inyectar. Cuando el émbolo se levanta, aumenta la sección liberada en las lumbreras, dejando así pasar más combustible hacia las válvulas de presión diferencial (cámaras superiores) y de estas hacia los inyectores. Al movimiento hacia arriba del émbolo de control se opone la fuerza que proviene del circuito de presión de mando. Esta presión de mando está regulada por el "regulador de la presión de mando" y sirve para asegurar que el émbolo de la válvula corredera sigue siempre inmediatamente el movimiento del plato-sonda sin que permanezca en posición alta cuando el plato-sonda vuelve a la posición de ralentí. Las válvulas de presión diferencial del dosificador-distribuidor de combustible aseguran el mantenimiento de una caída de presión constante entre los lados de entrada y de salida de las lumbreras. Esto significa que cualquier variación en la presión de línea del combustible o cualquier diferencia en la presión de apertura entre las inyectores no puede afectar el control del caudal de combustible.
Funcionamiento de la válvula corredera
La posición del émbolo de la válvula corredera en si es determinada por la posición del plato-sonda, por lo tanto esta en función del caudal de aire en el embudo del caudalimetro. El combustible debe ser repartido uniformemente entre los cilindros del motor. El principio de este reparto descansa en el mando de la sección de paso de las "rajas de estrangulación", mecanizadas en el cilindro de la "válvula corredera". El cilindro lleva tantas aperturas (rajas de estrangulamiento) como cilindros lleva el motor.
Una válvula de presión diferencial afectado a cada una de las rajas tiene la función de mantener en ellas una caída de presión de valor constante. Está válvula esta constituida por una cámara inferior y otra superior separadas por una membrana de acero. La presión reinante en la cámara superior es inferior a 0,1 bar (valor que representa la presión diferencial). Esta diferencia de presión se produce por un muelle helicoidal incorporado en la cámara superior. Si la cantidad de combustible que pasa a través de la cámara superior por las rajas de estrangulamiento se incrementa, la presión aumenta momentáneamente en esta cámara. La membrana de acero se encorva hacia la parte inferior y descubre la sección de salida hacia el inyector en la medida necesaria para que se establezca en la raja de estrangulamiento una presión diferencial de 0,1 bar. El embolo de la válvula corredera según su posición descubre mas o menos las rajas de estrangulamiento.
La posición del émbolo de la válvula corredera en si es determinada por la posición del plato-sonda, por lo tanto esta en función del caudal de aire en el embudo del caudalimetro. El combustible debe ser repartido uniformemente entre los cilindros del motor. El principio de este reparto descansa en el mando de la sección de paso de las "rajas de estrangulación", mecanizadas en el cilindro de la "válvula corredera". El cilindro lleva tantas aperturas (rajas de estrangulamiento) como cilindros lleva el motor.
Una válvula de presión diferencial afectado a cada una de las rajas tiene la función de mantener en ellas una caída de presión de valor constante. Está válvula esta constituida por una cámara inferior y otra superior separadas por una membrana de acero. La presión reinante en la cámara superior es inferior a 0,1 bar (valor que representa la presión diferencial). Esta diferencia de presión se produce por un muelle helicoidal incorporado en la cámara superior. Si la cantidad de combustible que pasa a través de la cámara superior por las rajas de estrangulamiento se incrementa, la presión aumenta momentáneamente en esta cámara. La membrana de acero se encorva hacia la parte inferior y descubre la sección de salida hacia el inyector en la medida necesaria para que se establezca en la raja de estrangulamiento una presión diferencial de 0,1 bar. El embolo de la válvula corredera según su posición descubre mas o menos las rajas de estrangulamiento.
El circuito de la presión de mando se deriva del circuito de alimentación por medio de un "orificio calibrado" situado en el dosificador-distribuidor. La presión de mando queda determinada por el regulador de presión de mando. El "estrangulamiento" que se sitúa por encima de la válvula corredera tiene la función de amortiguar los movimientos del plato-sonda ocasionados por las pulverizaciones de aire que se manifiestan a menudo a escasa velocidad.
Regulador de presión
Un regulador de presión de combustible situado en el regulador de mezcla (dosificador-distribuidor) mantiene una presión constante de 5 bar en la parte inferior de las válvulas de presión diferencial cualquiera que sea la fase de utilización del motor, o las variaciones de caudal de la bomba de alimentación. El regulador de presión devuelve el combustible sobrante al depósito con la presión atmosférica. También el regulador de presión devuelve al deposito el combustible que le llega del "regulador de fase de calentamiento" a través de la entrada (8) y pasando por la válvula de aislamiento (5).
Un regulador de presión de combustible situado en el regulador de mezcla (dosificador-distribuidor) mantiene una presión constante de 5 bar en la parte inferior de las válvulas de presión diferencial cualquiera que sea la fase de utilización del motor, o las variaciones de caudal de la bomba de alimentación. El regulador de presión devuelve el combustible sobrante al depósito con la presión atmosférica. También el regulador de presión devuelve al deposito el combustible que le llega del "regulador de fase de calentamiento" a través de la entrada (8) y pasando por la válvula de aislamiento (5).
Arranque en frío
Al arrancar en frío el motor necesita más combustible para compensar las pérdidas debidas a las condensaciones en las paredes frías del cilindro y de los tubos de admisión. Para compensar esta pérdida y para facilitar el arranque en frío, en el colector de admisión se ha instalado un inyector de arranque en frío (10), el cual inyecta gasolina adicional durante la fase de arranque. El inyector de arranque en frío se abre al activarse el devanado de un electroimán que se aloja en su interior. El interruptor térmico temporizado limita el tiempo de inyección de la válvula de arranque en frío de acuerdo con la temperatura del motor. A fin de limitar la duración máxima de inyección de el inyector de arranque en frío, el interruptor térmico temporizado va provisto de un pequeño elemento caldeable que se activa cuando se pone en marcha el motor de arranque. El elemento caldeable calienta una tira de bimetal que se dobla debido al calor y abre un par de contactos; así corta la corriente que va a el inyector de arranque en frío.
Al arrancar en frío el motor necesita más combustible para compensar las pérdidas debidas a las condensaciones en las paredes frías del cilindro y de los tubos de admisión. Para compensar esta pérdida y para facilitar el arranque en frío, en el colector de admisión se ha instalado un inyector de arranque en frío (10), el cual inyecta gasolina adicional durante la fase de arranque. El inyector de arranque en frío se abre al activarse el devanado de un electroimán que se aloja en su interior. El interruptor térmico temporizado limita el tiempo de inyección de la válvula de arranque en frío de acuerdo con la temperatura del motor. A fin de limitar la duración máxima de inyección de el inyector de arranque en frío, el interruptor térmico temporizado va provisto de un pequeño elemento caldeable que se activa cuando se pone en marcha el motor de arranque. El elemento caldeable calienta una tira de bimetal que se dobla debido al calor y abre un par de contactos; así corta la corriente que va a el inyector de arranque en frío.
Enriquecimiento para la fase de calentamiento
Mientras el motor se va calentando después de haber arrancado en frío, hay que compensar la gasolina que se condensa en las paredes frías de los cilindros y de los tubos de admisión. Durante la fase de calentamiento se enriquece la mezcla aire/combustible, pero es preciso reducir progresivamente este enriquecimiento a medida que se calienta el motor para evitar una mezcla demasiado rica. Para controlar la mezcla durante la fase de calentamiento se ha previsto un regulador de presión de mando (también llamado: regulador de fase de calentamiento) que regula la presión de mando. Una reducción de la presión de mando hace disminuir la fuerza antagonista en el medidor del caudal de aire, permitiendo así que el plato suba más en el embudo, y con ello se eleve la válvula de corredera dejando pasar más combustible por las lumbreras. En el interior del regulador de presión de mando una válvula de membrana (1) es controlada por un muelle helicoidal (4) a cuya fuerza se opone una lamina de bimetalica (3). Si el motor está frío, durante el calentamiento, la lamina bimetálica se curva hacia abajo debido a la resistencia calefactora (2) (que es alimentada durante la fase de calentamiento del motor) contrarrestando la fuerza del muelle (4) con lo que la membrana (1) se mueve de tal manera que la presión de mando sobre la válvula corredera disminuye fugandose la gasolina hacia el regulador de presión y de este al deposito, al disminuir la presión de mando sube la válvula corredera y aumenta la riqueza de la mezcla suministrada a los cilindros del motor.
Durante el arranque en frío la presión de mando es de 0,5 bar aproximadamente mientras que en condiciones normales se alcanza el valor de 3,7 bar.
Mientras el motor se va calentando después de haber arrancado en frío, hay que compensar la gasolina que se condensa en las paredes frías de los cilindros y de los tubos de admisión. Durante la fase de calentamiento se enriquece la mezcla aire/combustible, pero es preciso reducir progresivamente este enriquecimiento a medida que se calienta el motor para evitar una mezcla demasiado rica. Para controlar la mezcla durante la fase de calentamiento se ha previsto un regulador de presión de mando (también llamado: regulador de fase de calentamiento) que regula la presión de mando. Una reducción de la presión de mando hace disminuir la fuerza antagonista en el medidor del caudal de aire, permitiendo así que el plato suba más en el embudo, y con ello se eleve la válvula de corredera dejando pasar más combustible por las lumbreras. En el interior del regulador de presión de mando una válvula de membrana (1) es controlada por un muelle helicoidal (4) a cuya fuerza se opone una lamina de bimetalica (3). Si el motor está frío, durante el calentamiento, la lamina bimetálica se curva hacia abajo debido a la resistencia calefactora (2) (que es alimentada durante la fase de calentamiento del motor) contrarrestando la fuerza del muelle (4) con lo que la membrana (1) se mueve de tal manera que la presión de mando sobre la válvula corredera disminuye fugandose la gasolina hacia el regulador de presión y de este al deposito, al disminuir la presión de mando sube la válvula corredera y aumenta la riqueza de la mezcla suministrada a los cilindros del motor.
Durante el arranque en frío la presión de mando es de 0,5 bar aproximadamente mientras que en condiciones normales se alcanza el valor de 3,7 bar.
Con una carga de motor intermedia la depresión en el colector de admisión es suficiente para comprimir el muelle regulador de carga por lo que la membrana de la válvula de presión de mando (1) sube aumentando la presión de mando sobre la válvula de corredera por lo que se empobrece la mezcla que inyecta en los cilindros.
Válvula de aire adicional
Las resistencias por rozamiento del motor frío hacen necesario aumentar el caudal de aire/combustible mientras el motor se va calentando. Esto permite asimismo mantener un régimen de ralentí estable. La válvula de aire adicional se encarga de aumentar el caudal de aire en el motor mientras que el acelerador continúa en posición de ralentí. La válvula de aire adicional abre un conducto en bypass con la mariposa; como todo el aire que entra ha de pasar por el medidor del caudal de aire, el plato sube y deja pasar una cantidad de combustible proporcional por las lumbreras del distribuidor-dosificador de combustible. Una tira de bimetal controla el funcionamiento de la válvula de aire adicional al regular la sección de apertura del conducto de derivación. Al arrancar en frío queda libre una sección mayor que se va reduciendo a medida que aumenta la temperatura del motor, hasta que, finalmente, se cierra. Alrededor de la tira de bimetal hay un pequeño elemento caldeable que se conecta cuando el motor entra en funcionamiento. De este modo se controla el tiempo de apertura y el dispositivo no funciona si el motor está caliente porque la tira recibe la temperatura del motor.
Las resistencias por rozamiento del motor frío hacen necesario aumentar el caudal de aire/combustible mientras el motor se va calentando. Esto permite asimismo mantener un régimen de ralentí estable. La válvula de aire adicional se encarga de aumentar el caudal de aire en el motor mientras que el acelerador continúa en posición de ralentí. La válvula de aire adicional abre un conducto en bypass con la mariposa; como todo el aire que entra ha de pasar por el medidor del caudal de aire, el plato sube y deja pasar una cantidad de combustible proporcional por las lumbreras del distribuidor-dosificador de combustible. Una tira de bimetal controla el funcionamiento de la válvula de aire adicional al regular la sección de apertura del conducto de derivación. Al arrancar en frío queda libre una sección mayor que se va reduciendo a medida que aumenta la temperatura del motor, hasta que, finalmente, se cierra. Alrededor de la tira de bimetal hay un pequeño elemento caldeable que se conecta cuando el motor entra en funcionamiento. De este modo se controla el tiempo de apertura y el dispositivo no funciona si el motor está caliente porque la tira recibe la temperatura del motor.
Inyectores
El combustible dosificado por el dosificador-distribuidor, es enviado a los inyectores y de estos se inyecta en los diversos conductos de admisión antes de las válvulas de admisión de los cilindros del motor. Los inyectores están aislados del calor que genera el motor evitando la formación de pequeñas burbujas de vapor en los tubos de inyección después de parar el motor. La válvula (1) responde incluso a las cantidades pequeñas, lo cual asegura una pulverización adecuada incluso en régimen de ralentí
Los inyectores no contribuyen en la dosificación. Las válvulas de inyección se abren automáticamente cuando la presión sobrepasa un valor fijado (3,3 bar) y permanecen abiertas; inyectando gasolina mientras se mantiene la presión. La aguja de la válvula oscila a una frecuencia elevada obteniendose una excelente vaporización. Después del paro del motor los inyectores se cierran cuando la presión de alimentación es inferior a los 3,3 bar. Cuando se para el motor y la presión en el sistema de combustible desciende por debajo de la presión de apertura de la válvula de inyección un muelle realiza un cierre estanco que impide que pueda llegar ni una gota más a los tubos de admisión.
El combustible dosificado por el dosificador-distribuidor, es enviado a los inyectores y de estos se inyecta en los diversos conductos de admisión antes de las válvulas de admisión de los cilindros del motor. Los inyectores están aislados del calor que genera el motor evitando la formación de pequeñas burbujas de vapor en los tubos de inyección después de parar el motor. La válvula (1) responde incluso a las cantidades pequeñas, lo cual asegura una pulverización adecuada incluso en régimen de ralentí
Los inyectores no contribuyen en la dosificación. Las válvulas de inyección se abren automáticamente cuando la presión sobrepasa un valor fijado (3,3 bar) y permanecen abiertas; inyectando gasolina mientras se mantiene la presión. La aguja de la válvula oscila a una frecuencia elevada obteniendose una excelente vaporización. Después del paro del motor los inyectores se cierran cuando la presión de alimentación es inferior a los 3,3 bar. Cuando se para el motor y la presión en el sistema de combustible desciende por debajo de la presión de apertura de la válvula de inyección un muelle realiza un cierre estanco que impide que pueda llegar ni una gota más a los tubos de admisión.
Listado de una serie de marcas y modelos de vehículos que utilizan el sistema de inyección Bosch K-Jetronic
VEHÍCULO | SISTEMA | AÑO |
Audi 80/90/Coupe/Quattro
Audi 100/200 Quattro Audi 200 Turbo/200 Turbo Quattro Audi Quattro Audi 100 2.0 Ford Escort XR3i Ford Orion 1.6i Ford Sierra XR4i/Xr 4x4 Ford Granada 2.8i Ford Capri 2.8i Mercedes-Benz 230E/TE/CE (123) Mercedes-Benz 280SE/SEL (116) Mercedes-Benz 350SE/SEL (116) Mercedes-Benz 450 SE/SEL (116) Mercedes-Benz 280SE/SEL (126) Merc-Benz 380SE/SEL/SEC (126) Merc-Benz 500SE/SEL/SEC (126) Mercedes-Benz 280SL/SLC (107) Mercedes-Benz 350SL/SLC (107) Mercedes-Benz 380SL/SLC (107) Mercedes-Benz 450SLC (107) Mercedes-Benz 500SL/SLC (107) Renault 30 TX Saab 900 Saab 900 Turbo Volkswagen Golf/Jetta GTi Volkswagen Golf GTi 16V Volkswagen Jetta GTi 16V Volkswagen Passat GLi/GTi Volkswagen Passat/Santana 2.0 Volkswagen Passat/Santana 2.1 Volkswagen Passat 2.2 Volkswagen Passat GT Volkswagen Scirocco GTi Volvo 240/244/245/Turbo Volvo 740 |
Bosch
K-Jetronic |
1983-97
1984-88 1983-88 1980-87 1989-92 1982-90 1983-90 1983-88 1977-85 1981-87 1976-85 1976-80 1976-80 1975-80 1979-86 1979-86 1979-86 1974-86 1976-80 1979-86 1978-79 1978-81 1978-84 1979-91 1979-91 1976-90 1985-90 1985-90 1979-81 1983-87 1981-83 1985-87 1984 1976-90 1974-86 1984-90 |
kat: Catalizado
.
Inconvenientes
El fabricante Bosch lleva tiempo aplicando sus sistemas de inyección a los motores de inyección directa. Hace mas de 60 años en los motores de aviación y también en el renombrado Mercedes 300 SL del año 1954, con las puertas abatibles en forma de alas de mariposa. Este sistema de inyección funcionaba igual que el utilizado por los motores Diesel, es decir, estaba dotado de una bomba de inyección en linea que tiene tantos elementos de bombeo como cilindros tiene el motor y accionados por un árbol de levas sincronizado con el cigüeñal. La presión de inyección con la que trabajaba este sistema es de 15 a 20 kp/cm2, la cual si la comparamos frente a un Diesel (150 a 400) es muy baja, lo que hace que la precisión del equipo de bombeo no sea muy grande. Pero tenia el enorme inconveniente de la lubricación, ya que la gasolina no es lubricante, implica la necesidad de lubricar la bomba lo que encarece su fabricación. También los inyectores deben lubricarse, lo cual lo complica en extremo. Los inyectores que están en contacto con las altas presiones y la temperatura que se alcanza en la cámara de combustión del motor hacen que se deterioren rápidamente y requieren un gran mantenimiento por ello esta inyección directa solo se usaba en vehículos muy exclusivos o deportivos.
Por las razones expuestas anteriormente Bosch aparco el desarrollo de esta tecnología, hasta que la utilización masiva de la electrónica hizo mas fácil desarrollar un sistema lo suficientemente fiable y a un precio ajustado.
Modo homogéneo-pobre
El motor trabaja en el modo homogéneo-pobre durante la transición entre el modo estratificado y el homogéneo.
La mezcla pobre se encuentra distribuida de un modo homogéneo (uniforme) en la cámara de combustión. La relación de aire y combustible es de lambda 1,55, aproximadamente.
Nota: No es posible abrir al máximo la válvula de mariposa, porque debe existir siempre una cierta depresión en consideración del sistema de carbón activo y de la recirculación de gases de
escape.
Formación de la mezcla
El momento de inyección tan temprano permite disponer de más tiempo para la formación de la mezcla hasta el momento del encendido. De esa forma se produce un reparto homogéneo (uniforme) en la cámara de combustión.
Modo homogéneo
El modo homogéneo es comparable con el de funcionamiento de un motor con inyección en el colector de admisión.
La diferencia esencial consiste en que el combustible se inyecta directamente en el cilindro al tratarse de la versión de inyección directa de gasolina.
El par del motor viene determinado por el momento de encendido (corto plazo) y por la masa de aire aspirada (largo plazo). Para esta masa de aire se elige la cantidad necesaria a inyectar (lambda = 1).
Accionamiento
El eje de accionamiento de la bomba de combustible de alta presión es impulsado por el árbol de levas de admisión.
En el eje de accionamiento hay una leva excéntrica, que soporta un anillo de leva. Al girar el eje de accionamiento, la leva excéntrica con el anillo de leva establece los movimientos de ascenso y descenso del émbolo de la bomba.
Efectos en caso de avería
La válvula reguladora se encuentra cerrada al no tener la corriente aplicada. De ese modo se tiene establecido de que siempre esté disponible una presión suficiente del combustible.
Para proteger los componentes contra presiones excesivas se incorpora en la válvula reguladora de presión del combustible un limitador mecánico de la presión a través de un sistema de muelle. Abre al tener el combustible una presión de 120 bares.
Efectos en caso de avería
Un inyector averiado es reconocido por la detección de fallos de encendido/combustión y deja de ser excitado.
Funcionamiento
Durante el funcionamiento normal, la válvula se encuentra abierta y libera el paso hacia el regulador de presión del combustible.
Si durante el ciclo de arranque del motor la temperatura del líquido refrigerante supera los 110 °C y la temperatura del aire aspirado es superior a 50 °C se trata de un arranque en caliente. En ese caso, la unidad de control del motor excita la válvula durante unos 50 segundos y cierra así el paso hacia el regulador de presión
A raíz de ello aumenta la presión en el sistema de baja presión hasta alcanzar la presión de bombeo máxima de la bomba eléctrica. Por intervención de una válvula interna para la limitación de la presión, alcanza 5,8 bares como máximo.
Este aumento de presión impide que se produzcan burbujas de vapor en el lado aspirante de la bomba de alta presión y garantiza una alta presurización fiable.
de orden exterior son:
Previo cálculo del par teórico del motor se lleva a la práctica la solicitud por dos vías:
Funcionamiento
Aparte de los tres materiales estratificados platino, rodio y paladio, el catalizador-acumulador de NOx lleva una cuarta capa, que consta de óxido de bario. Esto permite almacenar interinamente óxidos
nítricos durante el funcionamiento con mezcla pobre.
La unidad de control para sensor de NOx
Se encuentra ubicada en los bajos del vehículo, cerca del sensor de NOx. Su emplazamiento cercano impide que las influencias parásitas externas falsifiquen las señales del sensor de NOx.
En la unidad de control para sensor de NOx se procesan las señales del sensor de NOx y se transmiten a la unidad de control del motor.
Inyección directa de gasolina
|
ObjetivosLas emisiones contaminantes de hidrocarburos, óxidos nítricos y monóxido de carbono se reducen hasta un 99% con la mediación de un catalizador de tres vías.
Por su parte, el dióxido de carbono (CO2) que se produce con motivo de la combustión, siendo el causante del «efecto invernadero», sólo se puede reducir a base de disminuir el consumo de combustible.
Teniendo en cuenta estos factores vemos que los sistemas de inyección con formación externa de la mezcla (inyección en el colector de admisión MPi) no sirven para cumplir estos objetivos, por eso la necesidad de desarrollar un sistema capaz de cumplir con estos compromisos. Este sistema es el motor de inyección directa de gasolina.
Con lo motores de inyección directa de gasolina se consiguen dos objetivos principales que estan vigentes para hoy y con vistas al futuro, estos objetivos son: reducir el consumo de combustible y con este también las emisiones contaminantes de escape.
Por su parte, el dióxido de carbono (CO2) que se produce con motivo de la combustión, siendo el causante del «efecto invernadero», sólo se puede reducir a base de disminuir el consumo de combustible.
Teniendo en cuenta estos factores vemos que los sistemas de inyección con formación externa de la mezcla (inyección en el colector de admisión MPi) no sirven para cumplir estos objetivos, por eso la necesidad de desarrollar un sistema capaz de cumplir con estos compromisos. Este sistema es el motor de inyección directa de gasolina.
Con lo motores de inyección directa de gasolina se consiguen dos objetivos principales que estan vigentes para hoy y con vistas al futuro, estos objetivos son: reducir el consumo de combustible y con este también las emisiones contaminantes de escape.
Las diferentes marcas de automóviles cada vez mas se están decidiendo por equipar sus modelos de gasolina con motores de inyección directa. Primero fue la marca japonesa Mitsubishi con los motores GDi, ahora le siguen Renault con los motores IDE, el grupo PSA con los motores HPi, y Volkswagen con los motores FSi.
Si comparamos el sistema de inyección en los colectores (inyección indirecta también llamados MPI) con la inyección directa de gasolina, entendemos porqué esta ultima es superior a la primera. Los inyectores de un motor de gasolina (MPI) suelen estar ubicados en el colector de admisión, lo que explica la denominación de estos sistemas. El combustible es inyectado por delante de una válvula cerrada o bien encima de la válvula abierta y es mezclado de forma casi completa con el aire de admisión en cada una de las toberas del colector de admisión. Pero esta mezcla de aire y neblina de combustible inyectado no permite su perfecta explosión en el cilindro si no está preparada conforme a una exacta relación estequiométrica comprendida en unos límites muy específicos (1/14,7). En el caso de los motores dotados de un catalizador de tres vías es válida la ideal ecuación de lambda igual a uno.
Esta precisa relación de aire/combustible tiene que ser ajustada durante cada uno de los ciclos del motor cuando la inyección tiene lugar en el colector de admisión. El problema de estos sistemas de inyección (indirecta) viene dado principalmente a cargas parciales del motor cuando el conductor solicite una potencia no muy elevada, por ejemplo, (acelerador a medio pisar). Los efectos se podrían comparar con una vela encendida dentro de un envase que se va tapando poco a poco por su apertura superior: la llama de la vela va desapareciendo conforme empeoran las condiciones de combustión. Esta especie de estrangulación supone un desfavorable comportamiento de consumo de un motor de ciclo Otto en los momentos de carga parcial.
Es aquí donde se declaran las grandes virtudes de la inyección directa de gasolina. Los inyectores de este sistema no están ubicados en las toberas de admisión, sino que están incorporados de forma estratégica con un determinado desplazamiento lateral por encima de las cámaras de combustión.
Es aquí donde se declaran las grandes virtudes de la inyección directa de gasolina. Los inyectores de este sistema no están ubicados en las toberas de admisión, sino que están incorporados de forma estratégica con un determinado desplazamiento lateral por encima de las cámaras de combustión.
La inyección directa de la gasolina posibilita una definición exacta de los intervalos de alimentación del carburante en cada ciclo de trabajo de los pistones así como un preciso control del tiempo que se necesita para preparar la mezcla de aire y combustible. En unas condiciones de carga parcial del motor, el combustible es inyectado muy cerca de la bujía y con una determinada turbulencia cilíndrica (efecto tumble) al final de la fase de compresión mientras el pistón se está desplazando hacia su punto muerto superior. Esta concentrada carga de mezcla puede ser explosionada aunque el motor se encuentre en esos momentos en una fase de trabajo con un determinado exceso de aire (1/12.4). Su grado de efectividad termodinámica es correspondientemente más alto. Comparado con un sistema de inyección en el colector de admisión (MPI) se obtienen unas importantes ventajas de consumo de combustible merced a la eliminación de la citada estrangulación.
Ventajas
- Desestrangulación en los modos operativos con mezcla "estratificada". En estos modos operativos se trabaja con un valor lambda comprendido entre 1,55 y 3. Esto permite abrir más la mariposa y aspirar mas aire, por que tiene que superar una menor resistencia que provocaba la valvula de mariposa al estar medio cerrada
- En el modo estratificado el motor trabaja con un valor lambda desde 1,6 hasta 3, consiguiendo una reducion de consumo de combustible considerable.
- Menores pérdidas de calor cedido a las paredes de los cilindros Esto es debido a que en el modo de mezcla "estratificada" la combustión únicamente tiene lugar en la zona próxima de la bujía, esto provoca menores pérdidas de calor cedido a la pared del cilindro, con lo cual aumenta el rendimiento térmico del motor.
- Debido al movimiento intenso de la mezcla en el modo homogéneo, el motor posee una alta compatibilidad con la recirculación de gases de escape, equivalente hasta un 25%.
Para aspirar la misma cantidad de aire fresco que cuando trabaja con bajos índices de recirculación de gases se procede a abrir la mariposa de gases un tanto más. De esa forma se aspira el aire superando una baja resistencia y disminuyen las pérdidas debidas a efectos de estrangulamiento.
- Con la inyección directa del combustible en el cilindro se extrae calor del aire de admisión, produciéndose un efecto de refrigeración de éste. La tendencia al picado se reduce, lo que permite aumentar a su vez la compresión. Una mayor relación de compresión conduce a una presión final superior en la fase de compresión, con lo cual también aumenta el rendimiento térmico del motor.
- Es posible reducir el régimen de ralentí, y se facilita el arranque en frío debido a que al reanudar la inyección el combustible no se deposita en las paredes de la cámara de combustión.
La mayor parte del combustible inyectado puede ser transformada de inmediato en energía utilizable. El motor funciona de un modo muy estable, incluso al trabajar con regímenes de
ralentí más bajos.
Inconvenientes
- Uno de los problemas principales que plantea la inyección directa de gasolina es el tratamiento de los gases de escape para cumplir las normativas anticontaminación. Los óxidos nítricos que se producen con motivo de la combustión en el modo "estratificado" y en el modo "homogéneo-pobre" no pueden ser transformados suficientemente en nitrógeno por medio de un catalizador convencional de tres vías. Sólo desde que ha sido desarrollado el catalizador-acumulador de NOx también se cumple la norma de emisiones de escape EU4 en estos modos operativos. Los óxidos nítricos se acumulan internamente en ese catalizador y se transforman en nitrógeno mediante medidas específicas para ello.
- Otro inconveniente reside en los problemas que plantea el azufre en la gasolina. Debido a la similitud química que tiene con respecto a los óxidos nítricos, el azufre también se almacena en el catalizador- acumulador de NOx y ocupa los sitios destinados a los óxidos nítricos. Cuanto mayor es el contenido de azufre en el combustible, tanto más frecuentemente se tiene que regenerar el catalizador-acumulador, lo cual consume combustible adicional.
En la gráfica inferior se compara distintas clases de gasolinas que hay en el mercado y se aprecia la influencia que tiene el contenido de azufre sobre la capacidad de acumulación del catalizador-acumulador de NOx.
La marca Mitsubishi fue la primera en construir motores de inyección directa de gasolina. En este motor la gasolina es inyectada directamente en el cilindro, con lo que se eliminan perdidas y se mejora el rendimiento. La cantidad exacta de gasolina se introduce con una temporización muy precisa, consiguiendo una combustión completa. Las innovaciones tecnológicas que presentan estos motores son:
- Colectores de admisión verticales.
- Pistones con una forma especial (deflector).
- Bomba de combustible de alta presión.
- Inyectores de alta presión.
- Colectores de admisión verticales.
- Pistones con una forma especial (deflector).
- Bomba de combustible de alta presión.
- Inyectores de alta presión.
Esquema general de funcionamiento
En la figura inferior tenemos el esquema general de los diferentes elementos que forman el sistema de inyección directa de gasolina. En el se ve el circuito de admisión de aire y el circuito de suministro de combustible.
El circuito de admisión de aire empieza con el sensor (1) encargado de medir la cantidad de aire que, en función de la carga, entra en el motor. También dispone de unas electroválvulas colocadas en by-pass en dicho circuito y que actúan; la (2) en compensación de la necesidad de aire adicional debido al accionamiento de elementos auxiliares del motor y la (3) en caso de un control de todo o nada. La válvula reguladora de ralentí (4) es la encargada de mantener el régimen de giro del motor constante y actúa controlando el paso del flujo de aire después de la mariposa. Finalmente, la válvula EGR (5) realiza la función de recircular los gases de escape cuando las altas temperaturas y presiones de combustión provocan la aparición de los peligrosos óxidos de nitrógeno en los gases de escape. Podemos ver también la posición vertical de los colectores de admisión que permiten, gracias a la longitud y su cuidado pulimentado, aumentar el rendimiento volumétrico.
En el circuito de suministro de combustible al motor la gasolina parte del depósito (6) gracias a una bomba previa (7) de baja presión que pasa por un filtro y un regulador de presión (8) y se conduce a un conjunto hidráulico (9) que incorpora una bomba de alta presión. Un conjunto regulador de alta presión (10) mantiene la presión de inyección en su ultimo tramo hacia el inyector (11). La bomba inyecta carburante a una presión de 50 bar y utiliza un sensor de presión de combustible para el control preciso de la alimentación. En el escape del motor se incorpora un convertidor catalítico (12) para eliminar los restos de NOx cuando el motor trabaje con mezcla pobre o estratificada.
En la figura inferior tenemos el esquema general de los diferentes elementos que forman el sistema de inyección directa de gasolina. En el se ve el circuito de admisión de aire y el circuito de suministro de combustible.
El circuito de admisión de aire empieza con el sensor (1) encargado de medir la cantidad de aire que, en función de la carga, entra en el motor. También dispone de unas electroválvulas colocadas en by-pass en dicho circuito y que actúan; la (2) en compensación de la necesidad de aire adicional debido al accionamiento de elementos auxiliares del motor y la (3) en caso de un control de todo o nada. La válvula reguladora de ralentí (4) es la encargada de mantener el régimen de giro del motor constante y actúa controlando el paso del flujo de aire después de la mariposa. Finalmente, la válvula EGR (5) realiza la función de recircular los gases de escape cuando las altas temperaturas y presiones de combustión provocan la aparición de los peligrosos óxidos de nitrógeno en los gases de escape. Podemos ver también la posición vertical de los colectores de admisión que permiten, gracias a la longitud y su cuidado pulimentado, aumentar el rendimiento volumétrico.
En el circuito de suministro de combustible al motor la gasolina parte del depósito (6) gracias a una bomba previa (7) de baja presión que pasa por un filtro y un regulador de presión (8) y se conduce a un conjunto hidráulico (9) que incorpora una bomba de alta presión. Un conjunto regulador de alta presión (10) mantiene la presión de inyección en su ultimo tramo hacia el inyector (11). La bomba inyecta carburante a una presión de 50 bar y utiliza un sensor de presión de combustible para el control preciso de la alimentación. En el escape del motor se incorpora un convertidor catalítico (12) para eliminar los restos de NOx cuando el motor trabaje con mezcla pobre o estratificada.
El colector de admisión vertical
Con este tipo de colector se consigue crear un flujo de aire en la admisión del tipo giratorio en sentido de las agujas del reloj, con el que se consigue un mayor rendimiento. La ventaja de este sistema de flujo giratorio respecto al turbulento utilizado en la manera clásica (inyección indirecta), es que en este ultimo tiende a concentrarse el combustible en la periferia del cilindro y por tanto alejado de la bujía, en cambio el giratorio permite concentrarlo en el lugar que mas interesa para una mejor combustión: alrededor de la bujía. El hecho de que se realice siguiendo el sentido horario obedece a la necesidad de evitar que por medio de la inyección directa de gasolina choque con la bujía, ya que esto crea una acumulación de hollín que provoca falsas explosiones. Si el flujo girara hacia la izquierda no daría el tiempo suficiente para conseguir que el chorro de gasolina inyectado directamente se vaporizase.
El ángulo relativamente grande del inyector ayuda a asegurar que también tendrá tiempo suficiente para que el chorro pulverizado se combustible se vaporice, incluso cuando se inyecta durante la carrera de compresión. El deflector del pistón ayuda a concentrar la mezcla de aire/gasolina rica alrededor de la bujía.
Esta mezcla estratificada de forma ideal, rica alrededor de la bujía, pobre en la periferia, permite que el motor GDI de Mitsubishi funcione suavemente en el modo de combustión ultra-pobre, con la asombrosa relación de aire 40/1, con lo cual se consigue una importante economía de combustible.
Con este tipo de colector se consigue crear un flujo de aire en la admisión del tipo giratorio en sentido de las agujas del reloj, con el que se consigue un mayor rendimiento. La ventaja de este sistema de flujo giratorio respecto al turbulento utilizado en la manera clásica (inyección indirecta), es que en este ultimo tiende a concentrarse el combustible en la periferia del cilindro y por tanto alejado de la bujía, en cambio el giratorio permite concentrarlo en el lugar que mas interesa para una mejor combustión: alrededor de la bujía. El hecho de que se realice siguiendo el sentido horario obedece a la necesidad de evitar que por medio de la inyección directa de gasolina choque con la bujía, ya que esto crea una acumulación de hollín que provoca falsas explosiones. Si el flujo girara hacia la izquierda no daría el tiempo suficiente para conseguir que el chorro de gasolina inyectado directamente se vaporizase.
El ángulo relativamente grande del inyector ayuda a asegurar que también tendrá tiempo suficiente para que el chorro pulverizado se combustible se vaporice, incluso cuando se inyecta durante la carrera de compresión. El deflector del pistón ayuda a concentrar la mezcla de aire/gasolina rica alrededor de la bujía.
Esta mezcla estratificada de forma ideal, rica alrededor de la bujía, pobre en la periferia, permite que el motor GDI de Mitsubishi funcione suavemente en el modo de combustión ultra-pobre, con la asombrosa relación de aire 40/1, con lo cual se consigue una importante economía de combustible.
Los motores de inyección directa gasolina funcionan con dos tipos de mezcla según sea la carga del motor: mezcla estratificada y mezcla homogénea.
Mezcla estratificada: el motor es alimentado con una mezcla poco enriquecida cuando el vehículo se desplaza en unas condiciones de carga parcial (pedal del acelerador a medio pisar). Para poder conseguir una mezcla pobre para alimentar el motor, éste debe ser alimentado de forma estratificada.
La mezcla de aire y combustible se concentra en torno a la bujía ubicada en una estratégica posición central en las cámaras de combustión, en cuyas zonas periféricas se acumula prácticamente sólo una capa de aire. Con esta medida se consigue la eliminación de la mencionada estrangulación para proporcionar un importante ahorro de combustible. La positiva característica de economía de consumo es también una consecuencia de la disminuida dispersión de calor. El aire concentrado de la manera comentada en la periferia del espacio de combustión mientras se produce la explosión de la mezcla en la zona central de la cámara proporciona una especie de aislamiento térmico. Con esta estratificación específica de la carga, el valor Lambda en el área de combustión oscila entre 1,5 y 3. De este modo, la inyección directa de gasolina alcanza en el campo de carga parcial el mayor ahorro de combustible frente a los inyecciones convencionales : en marcha de ralentí incluso un 40%.
La mezcla de aire y combustible se concentra en torno a la bujía ubicada en una estratégica posición central en las cámaras de combustión, en cuyas zonas periféricas se acumula prácticamente sólo una capa de aire. Con esta medida se consigue la eliminación de la mencionada estrangulación para proporcionar un importante ahorro de combustible. La positiva característica de economía de consumo es también una consecuencia de la disminuida dispersión de calor. El aire concentrado de la manera comentada en la periferia del espacio de combustión mientras se produce la explosión de la mezcla en la zona central de la cámara proporciona una especie de aislamiento térmico. Con esta estratificación específica de la carga, el valor Lambda en el área de combustión oscila entre 1,5 y 3. De este modo, la inyección directa de gasolina alcanza en el campo de carga parcial el mayor ahorro de combustible frente a los inyecciones convencionales : en marcha de ralentí incluso un 40%.
Durante la fase de admisión (1) figura inferior, el volumen de aire procedente de los colectores de admisión verticales recorre la superficie curvada del pistón (2) y refluye hacia arriba creando un potente flujo giratorio en el sentido de la agujas del reloj. El control del flujo es posible gracias a sensores de flujo de aire de tipo Karman, que controlan la contrapresión baja, y a dos selenoides de la válvula by-pass que permiten que grandes cantidades de aire lleguen al cilindro con suavidad, lo que es importantísimo cuando se trata de funcionar con relaciones de aire/combustible extremadamente pobres de hasta 40/1.
En la carrera de compresión del pistón la forma giratoria se descompone en pequeños y numerosos torbellinos. A continuación, en la ultima fase de la carrera de compresión, el inyector de turbulencia de alta presión pulveriza el combustible (3) siguiendo una espiral muy cerrada. Este movimiento de turbulencia junto con la elevada densidad del aire comprimido y los pequeños torbellinos, mantienen compacto el chorro pulverizado de combustible. El combustible se concentra alrededor de la bujía. La estratificación es muy buena: la mezcla aire/combustible es rica en el centro y pobre en la periferia.
Finalmente salta la chispa en la bujía (4) y el potente producto de la combustión es controlado por la cavidad esférica del pistón que se va extendiendo mediante una reacción en cadena. El resultado de todo este proceso es una mejora del 20% en el ahorro de combustible.
En la carrera de compresión del pistón la forma giratoria se descompone en pequeños y numerosos torbellinos. A continuación, en la ultima fase de la carrera de compresión, el inyector de turbulencia de alta presión pulveriza el combustible (3) siguiendo una espiral muy cerrada. Este movimiento de turbulencia junto con la elevada densidad del aire comprimido y los pequeños torbellinos, mantienen compacto el chorro pulverizado de combustible. El combustible se concentra alrededor de la bujía. La estratificación es muy buena: la mezcla aire/combustible es rica en el centro y pobre en la periferia.
Finalmente salta la chispa en la bujía (4) y el potente producto de la combustión es controlado por la cavidad esférica del pistón que se va extendiendo mediante una reacción en cadena. El resultado de todo este proceso es una mejora del 20% en el ahorro de combustible.
Mezcla homogénea: El control inteligente de la inyección permite disponer asimismo de una mezcla homogénea en los regímenes más elevados (cuando se exige potencia al motor). La inyección es adaptada de forma automática y el combustible no es inyectado en las fases de compresión sino en las de admisión. Unas determinadas leyes de la termodinámica imponen, no obstante, un aumento del llenado de los cilindros y una disminución de la temperatura de compresión en estas condiciones. Estos ajustes tienen unos efectos secundarios también muy positivos que se manifiestan en forma de unos elevados valores de potencia y par motor. Con una relación de compresión alta por encima de 11 (11,5:1) ofrece un valor significativamente más alto que un motor dotado de un sistema de inyección MPI (indirecta).
Con mezcla homogénea el combustible se inyecta durante al carrera de admisión para crear un efecto de refrigeración, el inyector de alta presión cambia la forma de funcionar en este modo para alimentar el combustible mediante un chorro largo en forma de cono, con objeto de conseguir una dispersión en el cilindro. El efecto de refrigeración evita las detonaciones o combustión espontánea en el cilindro que pueden producirse cuando el motor tiene una relación de compresión alta y con un elevado calentamiento.
Con mezcla homogénea el combustible se inyecta durante al carrera de admisión para crear un efecto de refrigeración, el inyector de alta presión cambia la forma de funcionar en este modo para alimentar el combustible mediante un chorro largo en forma de cono, con objeto de conseguir una dispersión en el cilindro. El efecto de refrigeración evita las detonaciones o combustión espontánea en el cilindro que pueden producirse cuando el motor tiene una relación de compresión alta y con un elevado calentamiento.
Reducción en las emisiones de gases contaminantes
Uno de los aspectos más importantes del motor GDI es la menor emisión de gases contaminantes (C02, NOx e hidrocarburos).
Si se quema gasolina se genera C02; por lo tanto, si se reduce la cantidad de gasolina quemada se reducirá también la cantidad de C02. De este modo, disminuyendo el consumo de combustible en un 20%, en el motor GDI descienden también las emisiones de C02 en ese mismo porcentaje.
Los catalizadores de tres vías no son eficaces en el motor GDI cuando funciona en el modo ultra-pobre de combustión. MITSUBISHI ha desarrollado un nuevo tipo de catalizador, denominado de reducción selectiva, para ayudar a disminuir las emisiones de monóxido de nitrógeno (NOx).
Uno de los aspectos más importantes del motor GDI es la menor emisión de gases contaminantes (C02, NOx e hidrocarburos).
Si se quema gasolina se genera C02; por lo tanto, si se reduce la cantidad de gasolina quemada se reducirá también la cantidad de C02. De este modo, disminuyendo el consumo de combustible en un 20%, en el motor GDI descienden también las emisiones de C02 en ese mismo porcentaje.
Los catalizadores de tres vías no son eficaces en el motor GDI cuando funciona en el modo ultra-pobre de combustión. MITSUBISHI ha desarrollado un nuevo tipo de catalizador, denominado de reducción selectiva, para ayudar a disminuir las emisiones de monóxido de nitrógeno (NOx).
El fabricante Bosch lleva tiempo aplicando sus sistemas de inyección a los motores de inyección directa. Hace mas de 60 años en los motores de aviación y también en el renombrado Mercedes 300 SL del año 1954, con las puertas abatibles en forma de alas de mariposa. Este sistema de inyección funcionaba igual que el utilizado por los motores Diesel, es decir, estaba dotado de una bomba de inyección en linea que tiene tantos elementos de bombeo como cilindros tiene el motor y accionados por un árbol de levas sincronizado con el cigüeñal. La presión de inyección con la que trabajaba este sistema es de 15 a 20 kp/cm2, la cual si la comparamos frente a un Diesel (150 a 400) es muy baja, lo que hace que la precisión del equipo de bombeo no sea muy grande. Pero tenia el enorme inconveniente de la lubricación, ya que la gasolina no es lubricante, implica la necesidad de lubricar la bomba lo que encarece su fabricación. También los inyectores deben lubricarse, lo cual lo complica en extremo. Los inyectores que están en contacto con las altas presiones y la temperatura que se alcanza en la cámara de combustión del motor hacen que se deterioren rápidamente y requieren un gran mantenimiento por ello esta inyección directa solo se usaba en vehículos muy exclusivos o deportivos.
Por las razones expuestas anteriormente Bosch aparco el desarrollo de esta tecnología, hasta que la utilización masiva de la electrónica hizo mas fácil desarrollar un sistema lo suficientemente fiable y a un precio ajustado.
El sistema de inyección directa de gasolina Bosch denominado MED trabaja según el principio de funcionamiento del Common Rail utilizado para la inyección diesel. Es decir, un conducto o regleta distribuidora común, de alta presión, alimenta con carburante todas las válvulas de inyección; la presión regulada en el conducto distribuidor de combustible la origina una bomba de alta presión que puede alcanzar presiones de hasta 120 bar. Con las válvulas de inyección accionadas de forma electromagnética, el inicio y la duración del proceso de inyección es variable dentro de amplios límites. El caudal de inyección se mide exactamente, mientras que la geometría del chorro está sincronizada con las exigencias del motor. La forma y el ángulo el chorro, así como el tamaño de las gotitas pulverizadas, constituyen también parámetros importantes para la formación de la mezcla y determinar valores de emisión bajas y consumos favorables.
Introducción al funcionamiento de este sistema de inyección
Como hemos visto en otros sistemas de inyección como el utilizado por la marca Japonesa Mitsubishi (GDI), a los dos modos operativos de funcionamiento del motor denominados: «carga estratificada» y «carga homogénea» se agrega un tercer modo, se trata del denominado "homogéneo-pobre". Con este modo operativo se reduce una vez más el consumo de combustible en comparación con el funcionamiento a lambda = 1 con recirculación de gases de escape. La unidad de control del motor elige el modo operativo en función de las condiciones de régimen /potencia / gases de escape y seguridad.
Modo estratificado
El motor funciona en el modo estratificado en los regímenes medios de carga y revoluciones.
La estratificación de la mezcla en la cámara de combustión permite que el motor trabaje con un valor lambda total de aprox. lambda = 1,6 hasta 3
El motor funciona en el modo estratificado en los regímenes medios de carga y revoluciones.
La estratificación de la mezcla en la cámara de combustión permite que el motor trabaje con un valor lambda total de aprox. lambda = 1,6 hasta 3
- En el centro de la cámara de combustión se encuentra una mezcla con buenas cualidades inflamables en torno a la bujía.
- Esta mezcla está rodeada de una capa exterior, que en el caso ideal está compuesta por aire fresco y gases de escape recirculados.
Modo homogéneo-pobre
El motor trabaja en el modo homogéneo-pobre durante la transición entre el modo estratificado y el homogéneo.
La mezcla pobre se encuentra distribuida de un modo homogéneo (uniforme) en la cámara de combustión. La relación de aire y combustible es de lambda 1,55, aproximadamente.
Modo homogéneo
A cargas y regímenes superiores, el motor funciona en el modo homogéneo.
La relación de aire y combustible en este modo operativo es de lambda = 1.
A cargas y regímenes superiores, el motor funciona en el modo homogéneo.
La relación de aire y combustible en este modo operativo es de lambda = 1.
En los modos homogéneo y homogéneo-pobre el combustible se inyecta en el cilindro durante el ciclo de admisión y se mezcla allí uniformemente con el aire aspirado, como se hace en los sistemas de inyección en el colector de admisión (MPi).
En el modo estratificado la mezcla de combustible y aire se dispone en la zona de la bujía (figura inferior) por medio del método de combustión por movimiento cilíndrico de la carga de gases guiado por pared y aire (movimiento tumble). El inyector está dispuesto de modo que el combustible sea proyectado sobre el rebaje específico en la cabeza del pistón (guiado por la pared) y desde ahí sea conducido en dirección hacia la bujía. Con el mando de la chapaleta en el colector de admisión y el rebaje de turbulencia se produce en el cilindro un movimiento cilíndrico del aire (tumble). Con este flujo de aire (conducido a su vez por aire) se respalda el transporte del combustible hacia la bujía. La formación de la mezcla se realiza en el trayecto hacia la bujía.
Modo de carga estratificada
Para que la gestión del motor cambie al modo estratificado tienen que estar cumplidas, entre otras cosas, ciertas premisas importantes:
Para que la gestión del motor cambie al modo estratificado tienen que estar cumplidas, entre otras cosas, ciertas premisas importantes:
- El motor se encuentra en el régimen de carga y revoluciones que corresponde
- En el sistema no existe ningún fallo de relevancia para los gases de escape
- La temperatura del líquido refrigerante supera los 50 °C
- El sensor de NOx está dispuesto para el funcionamiento
- La temperatura del catalizador-acumulador de NOx se halla entre los 250 °C y 500 °C
Si están cumplidas estas condiciones resulta posible poner en vigor el modo estratificado.
Admisión
En el modo estratificado se abre la mariposa lo más posible, para mantener reducidas las pérdidas por estrangulamiento.
La chapaleta en el colector de admisión cierra el conducto inferior en la culata. Debido a ello el aire de admisión se acelera y fluye describiendo un torbellino cilíndrico (tumble) a través del
conducto superior hacia el cilindro.
En el modo estratificado se abre la mariposa lo más posible, para mantener reducidas las pérdidas por estrangulamiento.
La chapaleta en el colector de admisión cierra el conducto inferior en la culata. Debido a ello el aire de admisión se acelera y fluye describiendo un torbellino cilíndrico (tumble) a través del
conducto superior hacia el cilindro.
Nota: No es posible abrir al máximo la válvula de mariposa, porque debe existir siempre una cierta depresión en consideración del sistema de carbón activo y de la recirculación de gases de
escape.
Flujo del aire
El flujo del aire describiendo un torbellino cilíndrico experimenta una intensificación en virtud de la geometría específica que tiene la cabeza del pistón.
El flujo del aire describiendo un torbellino cilíndrico experimenta una intensificación en virtud de la geometría específica que tiene la cabeza del pistón.
Inyección
La inyección (figura inferior) se realiza en el último tercio del ciclo de compresión. Comienza unos 60° y finaliza unos 45° antes del PMS de encendido.
El momento de la inyección ejerce una influencia importante sobre la posición que adopta la nube de la mezcla en la zona de la bujía.
La inyección (figura inferior) se realiza en el último tercio del ciclo de compresión. Comienza unos 60° y finaliza unos 45° antes del PMS de encendido.
El momento de la inyección ejerce una influencia importante sobre la posición que adopta la nube de la mezcla en la zona de la bujía.
El combustible se inyecta en dirección hacia el rebaje para combustible. La propagación deseada de la nube de mezcla se consigue gracias a la geometría del inyector.
Por el efecto del rebaje para combustible y el movimiento descendente del pistón se conduce el combustible en dirección hacia la bujía. Esta operación se intensifica por el caudal de aire con turbulencia cilíndrica, que conduce asimismo el combustible hacia la bujía. En el trayecto hacia la bujía se mezcla el combustible con el aire aspirado.
Formación de la mezcla
Para la formación de la mezcla en el modo estratificado solamente se dispone de un ángulo de cigüeñal de 40° a 50°. Esto es decisivo para la capacidad de ignición de la mezcla. Si el tiempo es más corto entre la inyección y el encendido, la mezcla no está preparada todavía lo suficiente para inflamarse de forma adecuada. Un tiempo más largo conduciría a una mayor homogeneización en toda la cámara de combustión.
Por ese motivo surge una nube de mezcla con una buena capacidad inflamable en el centro de la cámara de combustión, en torno a la bujía. Está rodeada de una capa exterior que, en el caso ideal, se compone de aire fresco y gases de escape recirculados.
La relación de aire y combustible en toda la cámara de combustión se halla entre: lambda = 1,6 y 3.
Para la formación de la mezcla en el modo estratificado solamente se dispone de un ángulo de cigüeñal de 40° a 50°. Esto es decisivo para la capacidad de ignición de la mezcla. Si el tiempo es más corto entre la inyección y el encendido, la mezcla no está preparada todavía lo suficiente para inflamarse de forma adecuada. Un tiempo más largo conduciría a una mayor homogeneización en toda la cámara de combustión.
Por ese motivo surge una nube de mezcla con una buena capacidad inflamable en el centro de la cámara de combustión, en torno a la bujía. Está rodeada de una capa exterior que, en el caso ideal, se compone de aire fresco y gases de escape recirculados.
La relación de aire y combustible en toda la cámara de combustión se halla entre: lambda = 1,6 y 3.
Combustión
Tras el posicionamiento exacto de la mezcla de combustible y aire en la zona de la bujía es cuando se produce el encendido. Durante esa operación sólo se inflama la nube de mezcla, mientras que los gases restantes actúan como un estrato aislante. Esto hace que se reduzcan las pérdidas de calor en las paredes y aumente el rendimiento térmico del motor. El momento de encendido se encuentra dentro de una estrecha ventana angular del cigüeñal, debido al final tardío de la inyección y al tiempo que transcurre para la formación de la mezcla al final del ciclo de compresión.
Tras el posicionamiento exacto de la mezcla de combustible y aire en la zona de la bujía es cuando se produce el encendido. Durante esa operación sólo se inflama la nube de mezcla, mientras que los gases restantes actúan como un estrato aislante. Esto hace que se reduzcan las pérdidas de calor en las paredes y aumente el rendimiento térmico del motor. El momento de encendido se encuentra dentro de una estrecha ventana angular del cigüeñal, debido al final tardío de la inyección y al tiempo que transcurre para la formación de la mezcla al final del ciclo de compresión.
Nota: El par generado por el motor viene determinado en este modo operativo únicamente a través de la cantidad de combustible inyectada. La masa de aire aspirada y el ángulo de encendido tienen aquí solamente poca importancia.
Modo de carga homogenero-pobreEstá modo de funcionamiento se sitúa entre el modo estratificado y el modo homogéneo. En toda la cámara de combustión existe aquí una mezcla homogénea-pobre. La relación de combustible y
aire es de aprox. lambda = 1,55. Rigen aquí las mismas premisas que para el modo estratificado.
aire es de aprox. lambda = 1,55. Rigen aquí las mismas premisas que para el modo estratificado.
Admisión
Igual que en el modo estratificado, la válvula de mariposa se encuentra lo más abierta posible y la chapaleta del colector de admisión está cerrada. Debido a ello se reducen por una parte las pérdidas por estrangulamiento y por otra se consigue un flujo intenso del aire en el cilindro.
Igual que en el modo estratificado, la válvula de mariposa se encuentra lo más abierta posible y la chapaleta del colector de admisión está cerrada. Debido a ello se reducen por una parte las pérdidas por estrangulamiento y por otra se consigue un flujo intenso del aire en el cilindro.
Inyección
El combustible se inyecta directamente en el cilindro a unos 300° APMS de encendido durante el ciclo de admisión. La unidad de control del motor se encarga de regular la cantidad inyectada de modo que la relación de combustible y aire sea de aproximadamente lambda = 1,55.
El combustible se inyecta directamente en el cilindro a unos 300° APMS de encendido durante el ciclo de admisión. La unidad de control del motor se encarga de regular la cantidad inyectada de modo que la relación de combustible y aire sea de aproximadamente lambda = 1,55.
Formación de la mezcla
El momento de inyección tan temprano permite disponer de más tiempo para la formación de la mezcla hasta el momento del encendido. De esa forma se produce un reparto homogéneo (uniforme) en la cámara de combustión.
Combustión
Igual que en el modo homogéneo, es posible elegir libremente el momento de encendido, porque se tiene un reparto homogéneo de la mezcla. La combustión se realiza en toda la cámara.
Igual que en el modo homogéneo, es posible elegir libremente el momento de encendido, porque se tiene un reparto homogéneo de la mezcla. La combustión se realiza en toda la cámara.
Modo homogéneo
El modo homogéneo es comparable con el de funcionamiento de un motor con inyección en el colector de admisión.
La diferencia esencial consiste en que el combustible se inyecta directamente en el cilindro al tratarse de la versión de inyección directa de gasolina.
El par del motor viene determinado por el momento de encendido (corto plazo) y por la masa de aire aspirada (largo plazo). Para esta masa de aire se elige la cantidad necesaria a inyectar (lambda = 1).
AdmisiónLa válvula de mariposa abre en función de la posición del acelerador. La chapaleta en el colector de admisión se mantiene abierta o cerrada según el punto operativo momentáneo.
- En la gama media de cargas y regímenes está cerrada la chapaleta en el colector de admisión, haciendo que el aire aspirado fluya describiendo un torbellino cilíndrico hacia el cilindro, lo cual actúa de forma positiva en la formación de la mezcla.
- A medida que sigue aumentando la carga y el régimen, la masa de aire que sólo se puede aspirar a través del canal superior ya no resultaría ser suficiente para el proceso. En ese caso la chapaleta en el colector de admisión abre también el paso del conducto inferior.
Inyección
El combustible se inyecta aproximadamente a los 300° APMS de encendido, directamente en el cilindro, durante el ciclo de admisión.
La energía necesaria para la evaporación del combustible se extrae del aire encerrado en la cámara de combustión, con lo cual el aire se enfría. Debido a ello es posible aumentar la relación de compresión en comparación con un motor con la inyección en el colector de admisión.
El combustible se inyecta aproximadamente a los 300° APMS de encendido, directamente en el cilindro, durante el ciclo de admisión.
La energía necesaria para la evaporación del combustible se extrae del aire encerrado en la cámara de combustión, con lo cual el aire se enfría. Debido a ello es posible aumentar la relación de compresión en comparación con un motor con la inyección en el colector de admisión.
Formación de la mezcla
Debido a la inyección del combustible durante el ciclo de admisión hay bastante tiempo disponible para la formación de la mezcla. Esto hace que en el cilindro se reparta una mezcla homogénea (uniforme), compuesta por el combustible inyectado y el aire aspirado.
La relación de combustible y aire en la cámara de combustión es de lambda = 1.
Debido a la inyección del combustible durante el ciclo de admisión hay bastante tiempo disponible para la formación de la mezcla. Esto hace que en el cilindro se reparta una mezcla homogénea (uniforme), compuesta por el combustible inyectado y el aire aspirado.
La relación de combustible y aire en la cámara de combustión es de lambda = 1.
Combustión
En el modo homogéneo se influye esencialmente con el momento de encendido sobre el par del motor, el consumo de combustible y el comportamiento de las emisiones de escape.
En el modo homogéneo se influye esencialmente con el momento de encendido sobre el par del motor, el consumo de combustible y el comportamiento de las emisiones de escape.
Inyección directa de gasolina, Bosch Motronic
|
Sistema de combustible, alimentación e inyección
El sistema de combustible está dividido en una parte de baja presión y en otra de alta presión.
- El sistema de combustible de baja presión: esta formado por un deposito (1), en su interior y sumergida una bomba eléctrica (2) eleva el combustible hacia un filtro (3) que se encarga de limpiarlo de impurezas, una vez filtrado el combustible se dirige a la bomba de alta presión (6). La presión del combustible en funcionamiento normal es de 3 bares y durante el arranque en caliente es de 5,8 bares como máximo.
Consta de:
1.- el depósito de combustible
2.- la bomba eléctrica de combustible
3.- el filtro de combustible
4.- la válvula de dosificación de combustible
5.- el regulador de presión del combustible (caída de presión)
- El sistema de combustible de alta presión: la bomba de alta presión (6) bombea el combustible hacia la rampa de inyección (8). La presión del combustible es medida allí por el sensor (9) correspondiente y la válvula reguladora se encarga de regularla desde 50 hasta 100 bares.
La inyección corre a cargo de los inyectores de alta presión (11)
Consta de:
6.- la bomba de combustible de alta presión
7.- tubería de alta presión
8.- rampa de inyección
9.- el sensor de presión del combustible
10.- la válvula reguladora para presión del combustible
11.- los inyectores de alta presión
Dentro del sistema de combustible encontramos como elemento secundario el depósito de carbón activo o Canister (12). Sirve para tratar los gases que genera el combustible en su almacenamiento en el depósito.
La bomba de combustible de alta presión
Tiene la función de suministrar el combustible a presión a la rampa de inyección. La bomba va atornillada a la carcasa del árbol de levas. Se trata de una bomba radial de 3 cilindros accionada por el árbol de levas de admisión (5). Con los tres elementos de bomba decalados a 120° se mantienen reducidas las fluctuaciones de la presión en la rampa de inyección de combustible.
Asume la función de establecer una presión de hasta 100 bares en el sistema de combustible de alta presión.
Tiene la función de suministrar el combustible a presión a la rampa de inyección. La bomba va atornillada a la carcasa del árbol de levas. Se trata de una bomba radial de 3 cilindros accionada por el árbol de levas de admisión (5). Con los tres elementos de bomba decalados a 120° se mantienen reducidas las fluctuaciones de la presión en la rampa de inyección de combustible.
Asume la función de establecer una presión de hasta 100 bares en el sistema de combustible de alta presión.
Accionamiento
El eje de accionamiento de la bomba de combustible de alta presión es impulsado por el árbol de levas de admisión.
En el eje de accionamiento hay una leva excéntrica, que soporta un anillo de leva. Al girar el eje de accionamiento, la leva excéntrica con el anillo de leva establece los movimientos de ascenso y descenso del émbolo de la bomba.
- Durante el movimiento descendente se aspira el combustible del sistema de baja presión.
- Durante el movimiento ascendente se bombea el combustible hacia la rampa de inyección..
Funcionamiento
El combustible pasa del sistema de baja hacia la bomba de alta presión. Allí recorre el émbolo hueco de la bomba hacia la válvula de admisión.
El combustible pasa del sistema de baja hacia la bomba de alta presión. Allí recorre el émbolo hueco de la bomba hacia la válvula de admisión.
- Carrera aspirante: Durante el movimiento descendente del émbolo de la bomba aumenta el volumen en su cilindro y la presión desciende. En cuanto la presión en el émbolo hueco es superior a la del cilindro de la
bomba, la válvula de admisión abre y permite que el combustible refluya.
- Carrera de bombeo: Con el comienzo del movimiento ascendente que efectúa el émbolo de la bomba aumenta la presión en su cilindro y la válvula de admisión
cierra. Si la presión en el cilindro de la bomba es superior a la de la rampa de inyección , la válvula de escape abre y el combustible es bombeado hacia la rampa de inyección.
Válvula reguladora de presión de combustible
Se encuentra atornillada entre la rampa de inyección y el tubo de retorno de combustible hacia el depósito.
Tiene la la función de controlar la presión en la rampa de inyección, independientemente de la cantidad inyectada y de la cantidad de combustible suministrado por la bomba.
Se encuentra atornillada entre la rampa de inyección y el tubo de retorno de combustible hacia el depósito.
Tiene la la función de controlar la presión en la rampa de inyección, independientemente de la cantidad inyectada y de la cantidad de combustible suministrado por la bomba.
Funcionamiento
Si se presentan diferencias con respecto a la presión teórica, la unidad de control del motor excita la válvula reguladora de la presión del combustible por medio de una señal modulada en anchura de los impulsos. A raíz de ello se crea un campo magnético en la bobina y la válvula con la bola de cierre despega de su asiento. En función de la magnitud de la señal se modifica de esta forma la sección de paso hacia el tubo de retorno y, con ésta, la cantidad de combustible que retorna, regulándose la presión correspondientemente.
Si se presentan diferencias con respecto a la presión teórica, la unidad de control del motor excita la válvula reguladora de la presión del combustible por medio de una señal modulada en anchura de los impulsos. A raíz de ello se crea un campo magnético en la bobina y la válvula con la bola de cierre despega de su asiento. En función de la magnitud de la señal se modifica de esta forma la sección de paso hacia el tubo de retorno y, con ésta, la cantidad de combustible que retorna, regulándose la presión correspondientemente.
Efectos en caso de avería
La válvula reguladora se encuentra cerrada al no tener la corriente aplicada. De ese modo se tiene establecido de que siempre esté disponible una presión suficiente del combustible.
Para proteger los componentes contra presiones excesivas se incorpora en la válvula reguladora de presión del combustible un limitador mecánico de la presión a través de un sistema de muelle. Abre al tener el combustible una presión de 120 bares.
Sensor de presión de combustible
El sensor de presión del combustible se encuentra atornillado en la rampa de inyección de combustible. Tiene la función de medir la presión del combustible en la rampa de inyección. Con esta medida la unidad de control del motor regula la presión del combustible en el sistema de alta presión, en función de una familia de curvas características.
El sensor de presión del combustible se encuentra atornillado en la rampa de inyección de combustible. Tiene la función de medir la presión del combustible en la rampa de inyección. Con esta medida la unidad de control del motor regula la presión del combustible en el sistema de alta presión, en función de una familia de curvas características.
Funcionamiento
A partir de la rampa de inyección fluye combustible hacia el sensor de presión.
A partir de la rampa de inyección fluye combustible hacia el sensor de presión.
- A baja presión del combustible sólo se deforma levemente la membrana de acero. De esa forma es alta la resistencia eléctrica que oponen las resistencias extensometricas y la tensión de la señal es baja.
- Si la presión del combustible es de alta magnitud, la membrana de acero se deforma en una medida intensa. Debido a ello es baja la resistencia eléctrica en las resistencias extensométricas y la tensión de la señal es correspondientemente alta.
La tensión de las señales se intensifica en el circuito electrónico y se transmite a la unidad de control del motor. La regulación de la presión del combustible se lleva a cabo con ayuda de la válvula reguladora de presión del combustible.
Efectos en caso de avería
Si se ausenta la señal del sensor de presión en el colector de admisión, la unidad de control del motor procede a excitar la válvula reguladora de la presión del combustible por medio de un
valor fijo.
Si se ausenta la señal del sensor de presión en el colector de admisión, la unidad de control del motor procede a excitar la válvula reguladora de la presión del combustible por medio de un
valor fijo.
Los inyectores de alta presión
Los inyectores van fijados a la culata e inyectan el combustible a alta presión directamente al interior del cilindro (inyección directa).
La misión de los inyectores es inyectar el combustible en un tiempo mínimo, adecuadamente pulverizado y de forma específica según el modo operativo momentáneo.
Así por ejemplo, en el modo estratificado se posiciona el combustible de forma concentrada en la zona de la bujía, mientras que en los modos homogéneo-pobre y homogéneo se pulveriza de un modo
uniforme en toda la cámara de combustión.
Los inyectores van fijados a la culata e inyectan el combustible a alta presión directamente al interior del cilindro (inyección directa).
La misión de los inyectores es inyectar el combustible en un tiempo mínimo, adecuadamente pulverizado y de forma específica según el modo operativo momentáneo.
Así por ejemplo, en el modo estratificado se posiciona el combustible de forma concentrada en la zona de la bujía, mientras que en los modos homogéneo-pobre y homogéneo se pulveriza de un modo
uniforme en toda la cámara de combustión.
Con un ángulo de proyección del chorro de 70° y un ángulo de inclinación del chorro de 20° se tiene dada un posicionamiento exacto del combustible, sobre todo en el modo estratificado.
Funcionamiento
Durante el ciclo de la inyección se excita el bobinado electromagnético en el inyector y se genera una campo magnético. A raíz de ello se atrae el inducido con la aguja, con lo cual abre el inyector y proyecta el combustible.
Al dejarse de excitar el bobinado se neutraliza el campo magnético y la aguja es oprimida por el muelle de compresión contra su asiento en el inyector. El flujo del combustible queda interrumpido.
Durante el ciclo de la inyección se excita el bobinado electromagnético en el inyector y se genera una campo magnético. A raíz de ello se atrae el inducido con la aguja, con lo cual abre el inyector y proyecta el combustible.
Al dejarse de excitar el bobinado se neutraliza el campo magnético y la aguja es oprimida por el muelle de compresión contra su asiento en el inyector. El flujo del combustible queda interrumpido.
Nota: podemos decir que los sistemas de inyección directa frente a los sistemas de inyección en el colector de admisión (inyección indirecta), tienen que trabajar con presiones de inyección mas altas y el tiempo disponible para hacer la inyección es notablemente menor. Sin embargo el mismo volumen de combustible puede ser inyectado en menos tiempo si se incrementa la presión de inyección. Como ejemplo orientativo diremos que en la inyección directa, el tiempo de inyección para 6.000 r.p.m. es de 5 ms frente a los 20 ms se los sistemas de inyección en el colector de admisión.
Excitación de los inyectores de alta presión
Los inyectores de alta presión se excitan por medio de un circuito electrónico en la unidad de control del motor.
Para que el inyector abra lo más rápidamente posible se le da una breve premagnetización y se le aplica una tensión de aprox. 90 voltios. De ahí resulta una intensidad de corriente de hasta 10 amperios. Al estar el inyector abierto al máximo resulta suficiente una tensión de 30 voltios y una intensidad de 3 a 4 amperios para mantenerlo abierto.
Los inyectores de alta presión se excitan por medio de un circuito electrónico en la unidad de control del motor.
Para que el inyector abra lo más rápidamente posible se le da una breve premagnetización y se le aplica una tensión de aprox. 90 voltios. De ahí resulta una intensidad de corriente de hasta 10 amperios. Al estar el inyector abierto al máximo resulta suficiente una tensión de 30 voltios y una intensidad de 3 a 4 amperios para mantenerlo abierto.
Efectos en caso de avería
Un inyector averiado es reconocido por la detección de fallos de encendido/combustión y deja de ser excitado.
La válvula dosificadora de combustibleEsta situada en el tubo de alimentación hacia la bomba de combustible de alta presión y hacia el regulador de presión del combustible. Va fijada a la torreta de la suspensión.
Funcionamiento
Durante el funcionamiento normal, la válvula se encuentra abierta y libera el paso hacia el regulador de presión del combustible.
Si durante el ciclo de arranque del motor la temperatura del líquido refrigerante supera los 110 °C y la temperatura del aire aspirado es superior a 50 °C se trata de un arranque en caliente. En ese caso, la unidad de control del motor excita la válvula durante unos 50 segundos y cierra así el paso hacia el regulador de presión
A raíz de ello aumenta la presión en el sistema de baja presión hasta alcanzar la presión de bombeo máxima de la bomba eléctrica. Por intervención de una válvula interna para la limitación de la presión, alcanza 5,8 bares como máximo.
Este aumento de presión impide que se produzcan burbujas de vapor en el lado aspirante de la bomba de alta presión y garantiza una alta presurización fiable.
Efectos en caso de avería
Si se avería la válvula dosificadora de combustible, un muelle de compresión la mantiene cerrada todo el tiempo. De esa forma aumenta la presión en el sistema de baja presión hasta 5,8 bares y se impide la inmovilización del vehículo durante el ciclo de arranque en caliente.
Si se avería la válvula dosificadora de combustible, un muelle de compresión la mantiene cerrada todo el tiempo. De esa forma aumenta la presión en el sistema de baja presión hasta 5,8 bares y se impide la inmovilización del vehículo durante el ciclo de arranque en caliente.
El depósito de carbón activo (canister)
Este dispositivo se necesita para cumplir con los requisitos legales planteados a las emisiones de hidrocarburos (HC). Evita que los vapores de combustible del depósito puedan pasar al medio ambiente. Los vapores de combustible se almacenan en el depósito de carbón activo y se conducen de forma sistemática hacia la cámara para su combustión.
Este dispositivo se necesita para cumplir con los requisitos legales planteados a las emisiones de hidrocarburos (HC). Evita que los vapores de combustible del depósito puedan pasar al medio ambiente. Los vapores de combustible se almacenan en el depósito de carbón activo y se conducen de forma sistemática hacia la cámara para su combustión.
- En los modos homogéneo-pobre y homogéneo: la mezcla capaz de ignición se encuentra distribuida de un modo uniforme en la cámara. La combustión tiene lugar en toda la extensión de la cámara, y el combustible procedente del depósito de carbón activo se quema en esa ocasión.
- En el modo estratificado: la mezcla capaz de ignición se encuentra concentrada solamente en la zona de la bujía. Una parte del combustible procedente del depósito de carbón activo se encuentra sin embargo en la zona exterior, no directamente inflamable. Esto puede provocar una combustión incompleta y aumentar las emisiones de HC en los gases de escape. Por tal motivo sólo se habilita el modo estratificado si el sistema calcula que el depósito de carbón activo tiene una carga baja.
La unidad de control del motor calcula la cantidad de combustible que se puede agregar procedente del depósito de carbón activo. Acto seguido se excita la electroválvula, efectuándose una adaptación de la cantidad inyectada y el reglaje de la mariposa. A esos efectos, la unidad de control del motor necesita la siguiente información:
- la carga del motor, procedente del medidor de la masa de aire por película caliente ,
- el régimen del motor, procedente del sensor de régimen del motor,
- la temperatura del aire aspirado, procedente del sensor de temperatura del aire aspirado y
- el estado de carga del depósito de carbón activo, procedente de la sonda Lambda
nyección directa de gasolina, Bosch Motronic
|
Sistema de admisión de aire
Ha sido adaptado a las necesidades de un motor de inyección directa de gasolina, en comparación con un sistema de inyección en el colector de admisión, el sistema influye de forma específica en el flujo del aire en el cilindro, según el modo operativo de funcionamiento del motor (modo estratificado, modo homogéneo, etc)
Los elementos básicos que forman el sistema de admisión de aire (figura inferior) son los siguientes:
- un medidor de la masa de aire por película caliente con el sensor de temperatura del aire aspirado (G42) para la determinación exacta de las condiciones de carga
- un sensor de presión en el colector de admisión para calcular la cantidad de gases de escape a recircular
- un circuito de mando para las chapaletas en el colector de admisión con objeto de conseguir un flujo específico del aire en el cilindro
- una electroválvula de recirculación de gases de escape con una gran sección de paso para conseguir altas cantidades de gases recirculados
- un sensor de presión para servofreno, destinado a regular la depresión de frenado.
- unidad de mando de la mariposa
- depósito de carbón activo
- unidad de control del motor
Acelerador electrónico
Constituye la condición previa esencial para la inyección directa de gasolina. Con su ayuda se puede regular la válvula de mariposa independientemente de la posición del acelerador y en los modos estratificado y homogéneo-pobre se la puede abrir a una mayor magnitud.
La ventaja se manifiesta en un funcionamiento del motor casi exento de pérdidas de estrangulamiento. Eso significa, que el motor tiene que aspirar el aire superando una menor resistencia, con lo cual se reduce el consumo de combustible.
Constituye la condición previa esencial para la inyección directa de gasolina. Con su ayuda se puede regular la válvula de mariposa independientemente de la posición del acelerador y en los modos estratificado y homogéneo-pobre se la puede abrir a una mayor magnitud.
La ventaja se manifiesta en un funcionamiento del motor casi exento de pérdidas de estrangulamiento. Eso significa, que el motor tiene que aspirar el aire superando una menor resistencia, con lo cual se reduce el consumo de combustible.
Funcionamiento
Los deseos expresados por el conductor a través del acelerador se detectan por medio de los sensores de posición del acelerador y se transmiten a la unidad de control del motor. Con ayuda de esta señal y otras señales suplementarias calcula el par necesario y lo implementa a través de los actuadores.
Los deseos expresados por el conductor a través del acelerador se detectan por medio de los sensores de posición del acelerador y se transmiten a la unidad de control del motor. Con ayuda de esta señal y otras señales suplementarias calcula el par necesario y lo implementa a través de los actuadores.
- En el modo estratificado se determina el par del motor a través de la cantidad de combustible.
La válvula de mariposa se encuentra casi completamente abierta, excepto un estrangulamiento necesario para el depósito de carbón activo, la recirculación de gases de escape y eventualmente para la regulación de la depresión para el freno. - En los modos homogéneo-pobre y homogéneo el par del motor se determina a través del ángulo de encendido y la masa de aire aspirada.
La válvula de mariposa abre de acuerdo con el par motor necesario.
Colector de admisión variable mediante trampillas (chapaletas)
Se utiliza para gestionar el flujo del aire en el cilindro de conformidad con el modo operativo reinante.
Se utiliza para gestionar el flujo del aire en el cilindro de conformidad con el modo operativo reinante.
Chapaleta en el colector de admisión accionada
En los modos estratificado y homogéneo-pobre y en partes del modo homogéneo se acciona la chapaleta en el colector de admisión y se cierra el conducto inferior en la culata.
Debido a ello el aire de admisión fluye únicamente a través del conducto superior hacia el cilindro. Este conducto está diseñado de modo que el aire de admisión ingrese describiendo una turbulencia cilíndrica. Adicionalmente aumenta la velocidad de flujo a través del estrecho conducto superior, intensificando la formación de la mezcla.
En los modos estratificado y homogéneo-pobre y en partes del modo homogéneo se acciona la chapaleta en el colector de admisión y se cierra el conducto inferior en la culata.
Debido a ello el aire de admisión fluye únicamente a través del conducto superior hacia el cilindro. Este conducto está diseñado de modo que el aire de admisión ingrese describiendo una turbulencia cilíndrica. Adicionalmente aumenta la velocidad de flujo a través del estrecho conducto superior, intensificando la formación de la mezcla.
Esto tiene dos ventajas
- En el modo estratificado, el flujo cilíndrico del aire transporta el combustible hacia la bujía. En el trayecto hacia ésta se realiza la formación de la mezcla.
- En el modo homogéneo-pobre y en partes del modo homogéneo, el flujo de turbulencia cilíndrica del aire respalda la formación de la mezcla. De esta forma se consigue una alta capacidad de ignición de la mezcla y una combustión estable, así como un funcionamiento con mezcla pobre.
Esto supone dos ventajas:
Chapaleta en el colector de admisión no accionada
Al funcionar a cargas y regímenes superiores en el modo homogéneo no se acciona la chapaleta en el colector de admisión, con lo cual se encuentran abiertos ambos conductos. Debido a la mayor sección de paso del conducto de admisión, el motor puede aspirar la masa de aire necesaria para la entrega de un par más intenso y una alta potencia.
Al funcionar a cargas y regímenes superiores en el modo homogéneo no se acciona la chapaleta en el colector de admisión, con lo cual se encuentran abiertos ambos conductos. Debido a la mayor sección de paso del conducto de admisión, el motor puede aspirar la masa de aire necesaria para la entrega de un par más intenso y una alta potencia.
Sensor de posición para la chapaleta en el colector de admisión
Va unido al eje para las chapaletas en el colector de admisión, y detecta la posición de las mismas, transmitiendo esta información a la unidad de control del motor. Esto es necesario, porque la actuación de las chapaletas en el colector de admisión influye en el encendido, en el contenido de gases residuales y en las pulsaciones del aire en el colector de admisión. La posición de las chapaletas en el colector de admisión resulta relevante por ello para los gases de escape, en virtud de lo cual se la tiene que verificar a través de la autodiagnosis. Este sensor es un potenciómetro
Efectos en caso de avería del sensor
Si se ausenta la señal del sensor ya sólo se permite el modo homogéneo.
Va unido al eje para las chapaletas en el colector de admisión, y detecta la posición de las mismas, transmitiendo esta información a la unidad de control del motor. Esto es necesario, porque la actuación de las chapaletas en el colector de admisión influye en el encendido, en el contenido de gases residuales y en las pulsaciones del aire en el colector de admisión. La posición de las chapaletas en el colector de admisión resulta relevante por ello para los gases de escape, en virtud de lo cual se la tiene que verificar a través de la autodiagnosis. Este sensor es un potenciómetro
Efectos en caso de avería del sensor
Si se ausenta la señal del sensor ya sólo se permite el modo homogéneo.
Electroválvula de control para chapaleta en el colector de admisión
Es excitada por la unidad de control del motor y abre el paso del depósito de vacío hacia la válvula neumática de accionamiento. A raíz de ello la válvula neumática se encarga de accionar las chapaletas en el colector de admisión.
Efectos en caso de avería de la electroválvula
Si se avería esta válvula ya sólo se permite el modo homogéneo.
Es excitada por la unidad de control del motor y abre el paso del depósito de vacío hacia la válvula neumática de accionamiento. A raíz de ello la válvula neumática se encarga de accionar las chapaletas en el colector de admisión.
Efectos en caso de avería de la electroválvula
Si se avería esta válvula ya sólo se permite el modo homogéneo.
Medidor de la masa de aire con sensor de temperatura del aire aspirado
Ambos sensores van alojados en una carcasa situada en el trayecto de admisión ante la unidad de mando de la mariposa.
Para obtener la señal más exacta posible sobre la carga del motor se emplea un medidor de la masa de aire por película caliente con detección de flujo inverso. Mide no sólo el aire aspirado, sino que también detecta la cantidad de aire que vuelve debido a la apertura y el cierre de las válvulas.
La temperatura del aire de admisión medida por el sensor se utiliza como valor de corrección.
Ambos sensores van alojados en una carcasa situada en el trayecto de admisión ante la unidad de mando de la mariposa.
Para obtener la señal más exacta posible sobre la carga del motor se emplea un medidor de la masa de aire por película caliente con detección de flujo inverso. Mide no sólo el aire aspirado, sino que también detecta la cantidad de aire que vuelve debido a la apertura y el cierre de las válvulas.
La temperatura del aire de admisión medida por el sensor se utiliza como valor de corrección.
Aplicaciones de la señal
Las señales se emplean para calcular todas las funciones supeditadas a la carga. Son éstas por ejemplo el tiempo de inyección, el momento de encendido y el sistema del depósito de carbón activo.
Las señales se emplean para calcular todas las funciones supeditadas a la carga. Son éstas por ejemplo el tiempo de inyección, el momento de encendido y el sistema del depósito de carbón activo.
Estructura
El medidor de la masa de aire por película caliente consta de una carcasa de material plástico con un conducto de medición y un circuito eléctrico con un elemento sensor. El conducto de medición está diseñado de modo que una parte del aire aspirado y el aire de flujo inverso pasen ante el elemento sensor.
En el elemento sensor se genera con ello una señal que se procesa en el circuito eléctrico y se transmite a la unidad de control del motor.
El medidor de la masa de aire por película caliente consta de una carcasa de material plástico con un conducto de medición y un circuito eléctrico con un elemento sensor. El conducto de medición está diseñado de modo que una parte del aire aspirado y el aire de flujo inverso pasen ante el elemento sensor.
En el elemento sensor se genera con ello una señal que se procesa en el circuito eléctrico y se transmite a la unidad de control del motor.
Efectos en caso de avería
Si se avería el medidor de la masa de aire se emplea la señal del sensor de presión en el colector de admisión como señal de carga del motor.
Si se avería el medidor de la masa de aire se emplea la señal del sensor de presión en el colector de admisión como señal de carga del motor.
Sensor de presión en el colector de admisión
Va fijado al colector de admisión. Mide la presión en el colector de admisión y transmite una señal correspondiente a la unidad de control del motor.
Va fijado al colector de admisión. Mide la presión en el colector de admisión y transmite una señal correspondiente a la unidad de control del motor.
Aplicaciones de la señal
Con esta señal y con las señales del medidor de la masa de aire y el sensor de temperatura del aire aspirado, la unidad de control del motor calcula la cantidad exacta de gases de escape a recircular.
Con el sensor de presión en el colector de admisión se detecta asimismo la carga durante el ciclo de arranque del motor, porque en esas condiciones son todavía demasiado inexactas las señales procedentes del medidor de la masa de aire, debido a las pulsaciones que presenta la admisión.
Con esta señal y con las señales del medidor de la masa de aire y el sensor de temperatura del aire aspirado, la unidad de control del motor calcula la cantidad exacta de gases de escape a recircular.
Con el sensor de presión en el colector de admisión se detecta asimismo la carga durante el ciclo de arranque del motor, porque en esas condiciones son todavía demasiado inexactas las señales procedentes del medidor de la masa de aire, debido a las pulsaciones que presenta la admisión.
Funcionamiento
La medición de la presión en el colector de admisión se realiza con ayuda de una membrana de cristales de silicio. Sobre esta membrana hay resistencias extensométricas, cuya resistencia eléctrica varía ante cualquier deformación de la membrana. El vacío de referencia se utiliza para la comparación de presiones.
La membrana se deforma según la intensidad de la presión en el colector de admisión, con lo cual varía la resistencia y se produce una variación de la tensión en la señal eléctrica. Con estas señales eléctricas, la unidad de control del motor detecta la presión que está dada en el colector de admisión.
La medición de la presión en el colector de admisión se realiza con ayuda de una membrana de cristales de silicio. Sobre esta membrana hay resistencias extensométricas, cuya resistencia eléctrica varía ante cualquier deformación de la membrana. El vacío de referencia se utiliza para la comparación de presiones.
La membrana se deforma según la intensidad de la presión en el colector de admisión, con lo cual varía la resistencia y se produce una variación de la tensión en la señal eléctrica. Con estas señales eléctricas, la unidad de control del motor detecta la presión que está dada en el colector de admisión.
Sistema de recirculación de gases de escape (EGR)
En la retroalimentación de los gases de escape se conduce una parte de los gases de escape a la admisión del motor. Hasta un cierto grado, una parte de los gases residuales creciente puede repercutir positivamente sobre la transformación de energía, reduciendo con ello la emisión de contaminantes.
En la retroalimentación de los gases de escape se conduce una parte de los gases de escape a la admisión del motor. Hasta un cierto grado, una parte de los gases residuales creciente puede repercutir positivamente sobre la transformación de energía, reduciendo con ello la emisión de contaminantes.
Así se determina la cantidad de gases de escape a recircular
Con ayuda del medidor de la masa de aire, la unidad de control del motor mide la masa del aire fresco aspirado y calcula de ahí la correspondiente presión en el colector de admisión. Si se alimentan gases de escape a través del sistema de recirculación aumenta la masa del aire fresco en una cantidad correspondiente a la de los gases recirculados y la presión en el colector de admisión aumenta.
El sensor de presión en el colector de admisión mide esta presión y transmite una señal de tensión correspondiente a la unidad de control del motor. Previo análisis de esta señal se determina la cantidad total (aire fresco + gases de escape). El sistema resta la masa de aire fresco de esta cantidad total y obtiene así la cantidad de gases de escape.
La ventaja reside en que se puede aumentar la cantidad de gases de escape a recircular y se la puede acercar aún más al límite operativo.
Con ayuda del medidor de la masa de aire, la unidad de control del motor mide la masa del aire fresco aspirado y calcula de ahí la correspondiente presión en el colector de admisión. Si se alimentan gases de escape a través del sistema de recirculación aumenta la masa del aire fresco en una cantidad correspondiente a la de los gases recirculados y la presión en el colector de admisión aumenta.
El sensor de presión en el colector de admisión mide esta presión y transmite una señal de tensión correspondiente a la unidad de control del motor. Previo análisis de esta señal se determina la cantidad total (aire fresco + gases de escape). El sistema resta la masa de aire fresco de esta cantidad total y obtiene así la cantidad de gases de escape.
La ventaja reside en que se puede aumentar la cantidad de gases de escape a recircular y se la puede acercar aún más al límite operativo.
Efectos en caso de avería
Si se avería el sensor de presión en el colector de admisión, la unidad de control del motor calcula la cantidad de gases de escape y reduce la cantidad a recircular en comparación con lo previsto en la familia de curvas características.
Si se avería el sensor de presión en el colector de admisión, la unidad de control del motor calcula la cantidad de gases de escape y reduce la cantidad a recircular en comparación con lo previsto en la familia de curvas características.
Sensor de presión para amplificación de servofreno
Se encuentra en el conducto entre el colector de admisión y el amplificador de servofreno. Mide la presión en el conducto y en el amplificador de servofreno, respectivamente.
Se encuentra en el conducto entre el colector de admisión y el amplificador de servofreno. Mide la presión en el conducto y en el amplificador de servofreno, respectivamente.
Aplicaciones de la señal
Con ayuda de la señal de tensión procedente del sensor de presión, la unidad de control del motor detecta si es suficiente la depresión para el funcionamiento del amplificador de servofreno.
Con ayuda de la señal de tensión procedente del sensor de presión, la unidad de control del motor detecta si es suficiente la depresión para el funcionamiento del amplificador de servofreno.
Funcionamiento
El amplificador de servofreno requiere una depresión específica para alcanzar lo más rápidamente posible la fuerza de frenado máxima.
En los modos operativos de carga estratificada y carga homogénea-pobre, la válvula de mariposa se encuentra más abierta y en el colector de admisión está dada una baja depresión. La depresión acumulada en el servofreno deja de ser suficiente si ahora se acciona el freno varias veces. Para evitar este fenómeno se procede a cerrar un poco más la válvula de mariposa, para que aumente el vacío
generado. Si la depresión sigue siendo insuficiente se cierra más aún la mariposa y en caso dado se pasa incluso al modo homogéneo.
El amplificador de servofreno requiere una depresión específica para alcanzar lo más rápidamente posible la fuerza de frenado máxima.
En los modos operativos de carga estratificada y carga homogénea-pobre, la válvula de mariposa se encuentra más abierta y en el colector de admisión está dada una baja depresión. La depresión acumulada en el servofreno deja de ser suficiente si ahora se acciona el freno varias veces. Para evitar este fenómeno se procede a cerrar un poco más la válvula de mariposa, para que aumente el vacío
generado. Si la depresión sigue siendo insuficiente se cierra más aún la mariposa y en caso dado se pasa incluso al modo homogéneo.
Inyección directa de gasolina, Bosch Motronic
|
Gestión electrónica del motor
Entradas
| Salidas
|
La unidad de control del motor va instalada en la caja de aguas y tiene 121 pines.
La unidad de control utilizada para motores de inyección directa es muy similar a las utilizadas en motores de inyección en colector de admisión. Por ejemplo Bosch en sus sistemas Motronic tiene la versión ME 7.5.10 se ve como en este caso le falta la D que es la que designaría que se trata un sistema de inyección directa de gasolina.
La unidad de control utilizada para motores de inyección directa es muy similar a las utilizadas en motores de inyección en colector de admisión. Por ejemplo Bosch en sus sistemas Motronic tiene la versión ME 7.5.10 se ve como en este caso le falta la D que es la que designaría que se trata un sistema de inyección directa de gasolina.
Dentro del sistema de inyección Motronic MED 7 hay varias versiones: MED 7.5.10 y MED 7.5.11. La diferencia principal entre ambas versiones es que la ultima posee un procesador mas rápido.
Gestión del motor basada en el par
El sistema Bosch Motronic MED 7.5.10/11 es un sistema de gestión de motores basado en el par. Esto significa, que se recogen, analizan y coordinan todas las solicitudes de entrega de par.
El sistema Bosch Motronic MED 7.5.10/11 es un sistema de gestión de motores basado en el par. Esto significa, que se recogen, analizan y coordinan todas las solicitudes de entrega de par.
Las solicitudes de entrega de par de orden interior son:
- arranque del motor
- calefacción del catalizador
- regulación del ralentí
- limitación de potencia
- limitación del régimen
- regulación lambda
de orden exterior son:
- deseos del conductor
- cambio automático (punto de cambio)
- sistema de frenos (regulación antideslizamiento de la tracción, regulación del par de inercia del motor)
- climatizador (compresor para climatizador On/Off)
- programador de velocidad
Previo cálculo del par teórico del motor se lleva a la práctica la solicitud por dos vías:
- En la primera vía se influye sobre el llenado de los cilindros. Sirve para las solicitudes de entrega de par de mayor plazo.
En el modo estratificado le corresponde poca importancia, porque la válvula de mariposa abre a una gran magnitud, para reducir las pérdidas por estrangulamiento. - En la segunda vía se influye por corto plazo sobre el par de giro, independientemente del llenado de los cilindros.
En el modo estratificado sólo se determina el par a través de la cantidad de combustible, mientras que en los modos homogéneo-pobre y homogéneo sólo se determina a través del momento de encendido.
Funcionamiento
Previo análisis de las solicitudes de entrega de par de orden interno y externo, la unidad de control del motor calcula el par teórico y la forma de ponerlo en práctica.
Previo análisis de las solicitudes de entrega de par de orden interno y externo, la unidad de control del motor calcula el par teórico y la forma de ponerlo en práctica.
Implementación en el modo estratificado
En el modo estratificado se implementa el par teórico a través de la cantidad inyectada. La masa de aire desempeña un papel de segunda importancia, porque la válvula de mariposa se encuentra abierta a una gran magnitud, para reducir las pérdidas por estrangulamiento.
Al momento de encendido le corresponde también una reducida importancia, debido a que la inyección se efectúa en un momento tardío.
En el modo estratificado se implementa el par teórico a través de la cantidad inyectada. La masa de aire desempeña un papel de segunda importancia, porque la válvula de mariposa se encuentra abierta a una gran magnitud, para reducir las pérdidas por estrangulamiento.
Al momento de encendido le corresponde también una reducida importancia, debido a que la inyección se efectúa en un momento tardío.
Implementación en el modo homogéneo-pobre y en el modo homogéneo
En estos dos modos operativos se implementan las solicitudes de entrega de par a corto plazo a través del momento de encendido y a largo plazo a través de la masa de aire.
En virtud de que la mezcla de combustible y aire corresponde a un factor lambda fijo de 1,55 o bien 1 en ambos modos operativos, la cantidad a inyectar viene dada por la masa del aire aspirado. Por ese motivo no se procede a regular aquí el par de giro.
En estos dos modos operativos se implementan las solicitudes de entrega de par a corto plazo a través del momento de encendido y a largo plazo a través de la masa de aire.
En virtud de que la mezcla de combustible y aire corresponde a un factor lambda fijo de 1,55 o bien 1 en ambos modos operativos, la cantidad a inyectar viene dada por la masa del aire aspirado. Por ese motivo no se procede a regular aquí el par de giro.
Sistema de encendidoAsume la función de inflamar la mezcla de combustible y aire en el momento adecuado. Para conseguir este objetivo es preciso que la unidad de control del motor determine el momento de encendido, la
energía de ignición y la duración que ha de tener la chispa del encendido en todos los puntos operativos. Con el momento de encendido se influye sobre el par del motor, el comportamiento de los gases de escape y el consumo de combustible del motor.
energía de ignición y la duración que ha de tener la chispa del encendido en todos los puntos operativos. Con el momento de encendido se influye sobre el par del motor, el comportamiento de los gases de escape y el consumo de combustible del motor.
- En el modo estratificado: es preciso que el momento de encendido se encuentre dentro de una estrecha ventana angular del cigüeñal, debido a las particularidades que caracterizan a la formación de la mezcla. Sólo así se inflama fiablemente esta mezcla.
- En los modos homogéneo-pobre y homogéneo: no existen diferencias con respecto a un motor en el que se inyecta la gasolina hacia el colector de admisión. Debido al reparto homogéneo de la mezcla se emplean en ambos sistemas de inyección unos momentos de encendido comparables entre sí.
El cálculo del momento de encendido óptimo se realiza mediante:
- la información principal:
1.- Carga del motor, procedente del medidor de la masa de aire y del sensor de temperatura del aire aspirado
2.- Régimen del motor, procedente del sensor de régimen del motor - la información de corrección
3.- Sensor de temperatura del líquido refrigerante
4.- Unidad de mando de la mariposa
5.- Sensor de picado
6.- Sensor de posición del acelerador
7.- Sonda lambda
Reglaje de distribución variable
Sistema que permite modificar los ángulos de apertura de las válvulas para aumentar el tiempo de llenado y vaciado del cilindro cuando el motor gira alto de vueltas y el tiempo disponible para ello es menor. Estos sistemas llamados "Convertidores de fase" permiten utilizar el tiempo óptimo de apertura y cierre de las válvulas a cualquier régimen de giro del motor
La recirculación interna de gases de escape se lleva a cabo por medio de un reglaje de distribución variable sin escalonamientos en el árbol de levas de admisión.
El reglaje se realiza en función de la carga y el régimen, abarcando un máximo de 40° ángulo de cigüeñal a partir de la posición básica en dirección de avance.
Sistema que permite modificar los ángulos de apertura de las válvulas para aumentar el tiempo de llenado y vaciado del cilindro cuando el motor gira alto de vueltas y el tiempo disponible para ello es menor. Estos sistemas llamados "Convertidores de fase" permiten utilizar el tiempo óptimo de apertura y cierre de las válvulas a cualquier régimen de giro del motor
La recirculación interna de gases de escape se lleva a cabo por medio de un reglaje de distribución variable sin escalonamientos en el árbol de levas de admisión.
El reglaje se realiza en función de la carga y el régimen, abarcando un máximo de 40° ángulo de cigüeñal a partir de la posición básica en dirección de avance.
Esto conduce a:
- una óptima recirculación interna de gases de escape, con la cual se reduce la temperatura de la combustión y disminuyen las emisiones de óxidos nítricos.
- un desarrollo más adecuado del par motor.
Señales de entrada para el calculo de ángulo de reglaje
1.- Medidor de masa de aire con sensor temperatura del aire
2.- Sensor de régimen motor
3.- Sensor de temperatura del liquido refrigerante
1.- Medidor de masa de aire con sensor temperatura del aire
2.- Sensor de régimen motor
3.- Sensor de temperatura del liquido refrigerante
Señal de entrada para conocer la posición efectiva de los árboles de levas
4.- Sensor Hall
4.- Sensor Hall
Señales de salida
5.- Válvula para reglaje de distribución variable.
5.- Válvula para reglaje de distribución variable.
Nota: si quieres saber mas sobre los convertidores de fase utilizados en los sistemas de distribución variable, visita el curso de nuestra web que trata este tema.
La recirculación de gases de escape
Es la que le da básicamente sentido al empleo de un catalizador-acumulador de NOx. Con ayuda de los gases de escape recirculados se reduce la temperatura de la combustión y se produce una menor cantidad de óxidos nítricos.
Esto permite que el catalizador pueda almacenar óxidos nítricos durante un período relativamente prolongado y que se pueda trabajar más sostenidamente con el modo estratificado y el homogéneo-pobre, ahorrando combustible.
La cantidad de gases de escape recirculados equivale como máximo a un 35% del total de gases de admisión.
Es la que le da básicamente sentido al empleo de un catalizador-acumulador de NOx. Con ayuda de los gases de escape recirculados se reduce la temperatura de la combustión y se produce una menor cantidad de óxidos nítricos.
Esto permite que el catalizador pueda almacenar óxidos nítricos durante un período relativamente prolongado y que se pueda trabajar más sostenidamente con el modo estratificado y el homogéneo-pobre, ahorrando combustible.
La cantidad de gases de escape recirculados equivale como máximo a un 35% del total de gases de admisión.
La recirculación de gases de escape se lleva a cabo:
- en el modo estratificado y en el modo homogéneo-pobre, siempre;
- en el modo homogéneo hasta 4.000 r.p.m. y a media carga, pero no al ralentí.
La válvula de recirculación de gases de escape
Esta sujeta y va atornillada al colector de admisión. Es de nuevo diseño para conseguir altos índices de recirculación de gases de escape.
Consta de una carcasa con una mariposa, un motor eléctrico y un potenciómetro para recirculación de gases de escape.
La toma de los gases de escape se realiza a través de un tubo de unión en la culata del cuarto cilindro. La unidad de control del motor excita el motor eléctrico en función de su familia de curvas características y acciona una mariposa.
Según la posición de la mariposa fluye ahora una determinada cantidad de gases de escape hacia el colector de admisión y se mezcla con el aire fresco aspirado.
El potenciómetro para recirculación de gases de escape en la tapa de la carcasa detecta la posición de la mariposa. De ese modo es posible diagnosticar las condiciones en que se encuentra la válvula de recirculación de gases de escape.
Esta sujeta y va atornillada al colector de admisión. Es de nuevo diseño para conseguir altos índices de recirculación de gases de escape.
Consta de una carcasa con una mariposa, un motor eléctrico y un potenciómetro para recirculación de gases de escape.
La toma de los gases de escape se realiza a través de un tubo de unión en la culata del cuarto cilindro. La unidad de control del motor excita el motor eléctrico en función de su familia de curvas características y acciona una mariposa.
Según la posición de la mariposa fluye ahora una determinada cantidad de gases de escape hacia el colector de admisión y se mezcla con el aire fresco aspirado.
El potenciómetro para recirculación de gases de escape en la tapa de la carcasa detecta la posición de la mariposa. De ese modo es posible diagnosticar las condiciones en que se encuentra la válvula de recirculación de gases de escape.
Inyección directa de gasolina, Bosch Motronic
|
Sistema de escape
El sistema de escape ha sido adaptado a las exigencias de un motor con inyección directa de gasolina. Hasta ahora era un gran problema el tratamiento de los gases de escape en motores con inyección
directa de gasolina. Esto se debe a que con un catalizador convencional de tres vías no se pueden alcanzar los límites legales de emisiones de óxidos nítricos en los modos estratificado, pobre y homogéneo-pobre. Por ello se incorpora para estos motores un catalizador-acumulador de NOx, que almacena los óxidos nítricos (NOx) en estos modos operativos. Al estar lleno el acumulador se pone en vigor un modo de regeneración, con el cual se desprenden los óxidos nítricos del catalizador-acumulador y se transforman en nitrógeno.
directa de gasolina. Esto se debe a que con un catalizador convencional de tres vías no se pueden alcanzar los límites legales de emisiones de óxidos nítricos en los modos estratificado, pobre y homogéneo-pobre. Por ello se incorpora para estos motores un catalizador-acumulador de NOx, que almacena los óxidos nítricos (NOx) en estos modos operativos. Al estar lleno el acumulador se pone en vigor un modo de regeneración, con el cual se desprenden los óxidos nítricos del catalizador-acumulador y se transforman en nitrógeno.
Nota: con la recirculación de gases de escape y el reglaje de distribución variable ya se reducen las emisiones de óxidos nítricos desde la propia combustión.
Refrigeración de los gases de escape
El objetivo consiste en refrigerar los gases de escape al grado que la temperatura en el catalizador-acumulador de NOx se mantenga lo más frecuente y prolongadamente posible dentro del margen
comprendido entre los 250 °C y 500 °C, puesto que sólo en este margen de temperaturas el catalizador-acumulador está en condiciones de almacenar los óxidos nítricos.
Otro motivo es el descenso permanente de la capacidad de acumulación si se calentó el catalizador-acumulador de NOx a más de 850 °C.
El objetivo consiste en refrigerar los gases de escape al grado que la temperatura en el catalizador-acumulador de NOx se mantenga lo más frecuente y prolongadamente posible dentro del margen
comprendido entre los 250 °C y 500 °C, puesto que sólo en este margen de temperaturas el catalizador-acumulador está en condiciones de almacenar los óxidos nítricos.
Otro motivo es el descenso permanente de la capacidad de acumulación si se calentó el catalizador-acumulador de NOx a más de 850 °C.
Refrigeración del colector de escape (sólo en algunas versiones de motor)
En el armazón delantero del vehículo se conduce aire fresco de forma específica hacia el colector de escape, reduciéndose así la temperatura de los gases de escape.
En el armazón delantero del vehículo se conduce aire fresco de forma específica hacia el colector de escape, reduciéndose así la temperatura de los gases de escape.
El tubo de escape de tres caudales
Se encuentra ante el catalizador-acumulador de NOx. Es la segunda medida que se aplica para reducir la temperatura de los gases de escape y con ésta la del catalizador-acumulador de NOx. Debido a la mayor superficie que representa, aumenta la disipación del calor hacia el aire del entorno y se reducen las temperaturas de los gases de escape.
Se encuentra ante el catalizador-acumulador de NOx. Es la segunda medida que se aplica para reducir la temperatura de los gases de escape y con ésta la del catalizador-acumulador de NOx. Debido a la mayor superficie que representa, aumenta la disipación del calor hacia el aire del entorno y se reducen las temperaturas de los gases de escape.
Ambas medidas conjuntas dan por resultado una reducción en la temperatura de los gases de escape, según la velocidad de marcha del vehículo, comprendida entre los 30 °C y 100 °C.
Sonda lambda de banda ancha
La sonda lambda de banda ancha va atornillada ante el catalizador en el colector de escape.
Se utiliza para determinar el contenido de oxígeno residual en los gases de escape.
La sonda lambda de banda ancha va atornillada ante el catalizador en el colector de escape.
Se utiliza para determinar el contenido de oxígeno residual en los gases de escape.
Aplicaciones de la señal
Con la sonda lambda de banda ancha es posible determinar con exactitud la relación de combustible y aire, también cuando difiere de lambda = 1.
En el modo homogéneo-pobre permite establecer de esa forma un lambda empobrecido de 1,55. En el modo estratificado se procede a determinar por cálculo el valor lambda, porque las sondas lambda de banda ancha son demasiado inexactas en este sector.
Con ayuda de la señal, la unidad de control del motor calcula el valor lambda efectivo e inicia la regulación al diferir con respecto al valor lambda teórico. La regulación se lleva a cabo a través de la cantidad inyectada.
Con la sonda lambda de banda ancha es posible determinar con exactitud la relación de combustible y aire, también cuando difiere de lambda = 1.
En el modo homogéneo-pobre permite establecer de esa forma un lambda empobrecido de 1,55. En el modo estratificado se procede a determinar por cálculo el valor lambda, porque las sondas lambda de banda ancha son demasiado inexactas en este sector.
Con ayuda de la señal, la unidad de control del motor calcula el valor lambda efectivo e inicia la regulación al diferir con respecto al valor lambda teórico. La regulación se lleva a cabo a través de la cantidad inyectada.
El catalizador previo de tres vías
Este catalizador va situado en el colector de escape. Debido a su posición cerca del motor alcanza rápidamente su temperatura de servicio y comienza con la depuración de los gases de escape. Esto permite respetar los estrictos valores límite impuestos a las emisiones de escape. Su misión es transformar catalíticamente los contaminantes de la combustión en sustancias inofensivas.
Este catalizador va situado en el colector de escape. Debido a su posición cerca del motor alcanza rápidamente su temperatura de servicio y comienza con la depuración de los gases de escape. Esto permite respetar los estrictos valores límite impuestos a las emisiones de escape. Su misión es transformar catalíticamente los contaminantes de la combustión en sustancias inofensivas.
Funcionamiento
- Modo homogéneo con lambda = 1
Los hidrocarburos (HC) y los monóxidos de carbono (CO) reaccionan con el oxígeno (O) de los óxidos nítricos (NOx), transformándose en agua (H2O) y en dióxido de carbono (CO2). Los óxidos nítricos se reducen al mismo tiempo formando nitrógeno (N2). - En el modo estratificado y en el modo homogéneo-pobre con lambda > 1
Los hidrocarburos y los monóxidos de carbono reaccionan preferentemente con el oxígeno que abunda en los gases de escape y no con los óxidos nítricos. Por ese motivo, los óxidos nítricos no son transformados en nitrógeno en un catalizador de tres vías durante el modo de mezcla pobre. Pasan a través del catalizador de tres vías haca el catalizador-acumulador de NOx.
Sensor de temperatura de los gases de escape
El sensor de temperatura de los gases de escape va atornillado en el tubo de escape detrás del precatalizador.
Mide la temperatura de los gases de escape y transmite esta información a la unidad de control del motor.
El sensor de temperatura de los gases de escape va atornillado en el tubo de escape detrás del precatalizador.
Mide la temperatura de los gases de escape y transmite esta información a la unidad de control del motor.
Aplicaciones de la señal
Con ayuda de la señal procedente del sensor de temperatura de los gases de escape, la unidad de control del motor calcula, entre otras cosas, la temperatura en el catalizador-acumulador de NOx.
Con ayuda de la señal procedente del sensor de temperatura de los gases de escape, la unidad de control del motor calcula, entre otras cosas, la temperatura en el catalizador-acumulador de NOx.
Esto resulta necesario por los motivos siguientes:
- El catalizador-acumulador de NOx sólo puede almacenar óxidos nítricos a una temperatura operativa entre los 250 °C y 500 °C. Por ello, sólo en este margen de temperaturas se puede pasar a los modos estratificado y homogéneo-pobre.
- El azufre se almacena interinamente en el catalizador-acumulador de NOx. Para desprender nuevamente el azufre en los puntos de retención es preciso que la temperatura en el catalizador-acumulador sea de 650 °C como mínimo.
Funcionamiento
En el sensor se encuentra una resistencia de medición con coeficiente negativo de temperatura (NTC). Eso significa, que a medida que aumenta la temperatura se reduce su resistencia y la tensión de la señal aumenta. Esta tensión de la señal está asignada a una temperatura específica en la unidad de control del motor.
En el sensor se encuentra una resistencia de medición con coeficiente negativo de temperatura (NTC). Eso significa, que a medida que aumenta la temperatura se reduce su resistencia y la tensión de la señal aumenta. Esta tensión de la señal está asignada a una temperatura específica en la unidad de control del motor.
Efectos en caso de avería del sensor
Si se ausenta esta señal se pasa a la función de emergencia y la unidad de control del motor calcula la temperatura de los gases de escape. En virtud de que este cálculo no es tan exacto, el sistema pasa más temprano al modo homogéneo.
Si se ausenta esta señal se pasa a la función de emergencia y la unidad de control del motor calcula la temperatura de los gases de escape. En virtud de que este cálculo no es tan exacto, el sistema pasa más temprano al modo homogéneo.
Catalizador-acumulador de NOxVa instalado en el mismo sitio que un catalizador principal de tres vías, de tipo convencional. Desempeña las funciones de un catalizador de tres vías y puede almacenar adicionalmente óxidos nítricos.
Misión
- En el modo homogéneo con lambda = 1, el catalizador-acumulador de NOx trabaja como un catalizador convencional de tres vías.
- En los modos estratificado y homogéneo-pobre con lambda > 1 ya no puede efectuar la conversión de los óxidos nítricos. Por ello se los almacena en el catalizador-acumulador de NOx. Una vez agotada la capacidad de acumulación se efectúa un ciclo de regeneración. Debido a la similitud química con los óxidos nítricos también almacena el azufre.
Funcionamiento
Aparte de los tres materiales estratificados platino, rodio y paladio, el catalizador-acumulador de NOx lleva una cuarta capa, que consta de óxido de bario. Esto permite almacenar interinamente óxidos
nítricos durante el funcionamiento con mezcla pobre.
- Acumulación
Los óxidos nítricos se oxidan en el estrato de platino, formando dióxido nítrico y reaccionan entonces con el óxido de bario formando nitrato bárico.
- Desacumulación (regeneración)
La desacumulación se lleva a cabo por ejemplo por medio de las moléculas de CO que abundan en los gases de escape correspondientes a mezcla rica.
Primero se reduce el nitrato bárico nuevamente a óxido de bario, por la reacción con el monóxido de carbono. De esa forma se despiden dióxido de carbono y monóxido de nitrógeno. La presencia de rodio y platino hace que se reduzcan los óxidos nítricos, produciendo nitrógeno, y que el monóxido de carbono se oxide produciendo dióxido de carbono.
La unidad de control para sensor de NOx
Se encuentra ubicada en los bajos del vehículo, cerca del sensor de NOx. Su emplazamiento cercano impide que las influencias parásitas externas falsifiquen las señales del sensor de NOx.
En la unidad de control para sensor de NOx se procesan las señales del sensor de NOx y se transmiten a la unidad de control del motor.
Efectos en caso de avería
Si se avería la unidad de control para sensor de NOx, el sistema pasa de regulación a control.
Debido a las mayores emisiones de óxidos nítricos se prohiben los modos estratificado y homogéneo-pobre.
Si se avería la unidad de control para sensor de NOx, el sistema pasa de regulación a control.
Debido a las mayores emisiones de óxidos nítricos se prohiben los modos estratificado y homogéneo-pobre.
Sensor de NOx
Va atornillado en el tubo de escape, directamente detrás del catalizador-acumulador de NOx. En éste se determina el óxido nítrico (NOx) y el contenido de oxígeno en los gases de escape y se transmiten las señales correspondientes a la unidad de control para sensor de NOx.
Va atornillado en el tubo de escape, directamente detrás del catalizador-acumulador de NOx. En éste se determina el óxido nítrico (NOx) y el contenido de oxígeno en los gases de escape y se transmiten las señales correspondientes a la unidad de control para sensor de NOx.
Estructura
Consta de dos cámaras, dos celdas de bomba, varios electrodos y una calefacción. El elemento sensor consta a su vez de dióxido de circonio.
El circonio presenta la particularidad de que, al tener una tensión aplicada, los iones negativos de oxígeno del electrodo negativo se desplazan hacia el electrodo positivo.
Consta de dos cámaras, dos celdas de bomba, varios electrodos y una calefacción. El elemento sensor consta a su vez de dióxido de circonio.
El circonio presenta la particularidad de que, al tener una tensión aplicada, los iones negativos de oxígeno del electrodo negativo se desplazan hacia el electrodo positivo.
Aplicaciones de la señal
Con ayuda de estas señales se detecta y comprueba:
Con ayuda de estas señales se detecta y comprueba:
- si es correcto el funcionamiento del catalizador.
- si es correcto el punto de regulación lambda = 1 de la sonda lambda de banda ancha en el precatalizador o si se tiene que corregir. La corrección se puede llevar a cabo a través de un circuito interno en la unidad de control para NOx. Con su ayuda se puede captar en los electrodos del sensor de NOx una señal parecida a la de la sonda de señales a saltos.
Una señal de esa índole es muy exacta dentro del margen lambda = 1. - cuándo está agotada la capacidad de acumulación en el catalizador-acumulador de NOx y cuándo se tiene que iniciar un ciclo de regeneración de NOx o de azufre.
Las señales son transmitidas por el sensor de NOx a la unidad de control para sensor de NOx.
Efectos en caso de avería
Si se ausenta la señal del sensor de NOx ya sólo se permite trabajar el motor en el modo homogéneo.
Efectos en caso de avería
Si se ausenta la señal del sensor de NOx ya sólo se permite trabajar el motor en el modo homogéneo.
Funcionamiento
El funcionamiento del sensor de NOx se basa en la medición de oxígeno y se puede derivar del de una sonda lambda de banda ancha.
El funcionamiento del sensor de NOx se basa en la medición de oxígeno y se puede derivar del de una sonda lambda de banda ancha.
- Determinación del factor lambda en la primera cámara
Una parte de los gases de escape fluye hacia la 1ª cámara. Debido a que existen diferentes contenidos de oxígeno en los gases de escape y en la celda de referencia resulta mensurable una tensión eléctrica en los electrodos. La unidad de control para sensor de NOx se encarga de regular esta tensión a 425 mV constantes. Esto equivale a una relación de combustible y aire de lambda = 1. Si existen diferencias se extrae o introduce oxígeno. La corriente necesaria de la bomba constituye una medida para el valor lambda. - Determinación del contenido de NOx en la segunda cámara
Los gases de escape exentos de oxígeno fluyen de la 1ªa la 2ª cámara. Las moléculas de NOx en el gas de escape se disocian en un electrodo especial, produciendo N2 y O2. En virtud de que en los electrodos interior y exterior se regula una tensión constante de 450 mV, los iones de oxígeno se desplazan del electrodo interior hacia el exterior. La corriente de bomba de oxígeno que fluye por ese motivo constituye una medida para determinar el contenido de oxígeno en la 2ª cámara. Como la corriente de bomba de oxígeno guarda la misma relación hacia el contenido de óxidos nítricos en los gases de escape resulta posible determinar así la cantidad de óxidos nítricos.
Si el contenido de óxidos nítricos sobrepasa un valor umbral específico queda agotada la capacidad de almacenamiento en el catalizador-acumulador de NOx y se inicia un ciclo de regeneración de NOx.
Si este valor umbral se sobrepasa en intervalos de tiempo cada vez más breves, significa que el catalizador-acumulador está saturado de azufre y se inicia por ello un ciclo de regeneración de azufre.
Modo de regeneración
En este modo se desprenden los óxidos nítricos y el azufre que se encuentran incrustados en el catalizador-acumulador de NOx y se transforman en nitrógeno no tóxico y dióxido de azufre respectivamente.
Si este valor umbral se sobrepasa en intervalos de tiempo cada vez más breves, significa que el catalizador-acumulador está saturado de azufre y se inicia por ello un ciclo de regeneración de azufre.
Modo de regeneración
En este modo se desprenden los óxidos nítricos y el azufre que se encuentran incrustados en el catalizador-acumulador de NOx y se transforman en nitrógeno no tóxico y dióxido de azufre respectivamente.
- La regeneración de óxidos nítricos
Se lleva a cabo cuando la concentración de óxidos nítricos sobrepasa un valor específico detrás del catalizador-acumulador. A raíz de ello, la unidad de control del motor detecta que el catalizador ya no puede almacenar más óxidos nítricos y está agotada la capacidad de acumulación. A consecuencia de ello se activa el modo de regeneración.
Con motivo de esta operación el sistema pasa del modo estratificado pobre a un modo homogéneo ligeramente enriquecido, aumentando así el contenido de hidrocarburos y monóxido de carbono en los gases de escape.
En el catalizador-acumulador se combinan estas dos sustancias con el oxígeno de los óxidos nítricos y éstos se transforman en nitrógeno.
El catalizador-acumulador de NOx puede almacenar óxidos nítricos durante un máximo de 90 segundos en el modo estratificado. Después de ello se realiza una regeneración durante unos 2 segundos.
- La regeneración de azufre
Es una operación más compleja, porque el azufre es más resistente a efectos de temperatura y permanece en el catalizador durante la regeneración de óxidos nítricos.
El sistema efectúa un ciclo de desulfuración cuando la capacidad del catalizador-acumulador de NOx se agota en intervalos de tiempo cada vez más breves.
De esta particularidad, la unidad de control del motor detecta que los puntos de retención del azufre están ocupados y que ya no se pueden almacenar óxidos nítricos.
En ese momento y a partir de una velocidad mínima específica del vehículo se procede durante unos 2 minutos:
- a pasar al modo homogéneo y
- a subir la temperatura del catalizador-acumulador a más de 650 °C a base de retrasar el momento de encendido.
Sólo entonces reacciona el azufre acumulado y se transforma en dióxido de azufre (SO2).
Al circular con cargas y regímenes superiores se produce automáticamente el ciclo de desulfuración, porque se circula en el modo homogéneo y se alcanza así la temperatura necesaria para la desulfuración en el catalizador-acumulador de NOx.
Nota: para mantener lo más reducido posible el consumo de combustible durante el ciclo de regeneración de azufre se recomienda repostar un combustible exento de azufre (p. ej. Shell Optimax).
No hay comentarios:
Publicar un comentario